In the field of Quality, Measurement System Analysis (MSA) plays a important role to ensure the accuracy of the measurement.
It is one of among 5 quality core tools.
Whether it’s in manufacturing, healthcare, or any other industry, understanding the importance of measuring system analysis is essential for good quality of products.
However, many companies are struggle with this.
That’s why we have created this step-by-step guide to understand the basics of measurement variation and measurement system analysis, this guide covers everything you need to know.
By following this guide, you will be able to identify and eliminate sources of measurement error, improve process control, reduce variation, and maintain the overall quality of your products or services.
let’s dive in.

What is Measurement System?
Every decision taken in our organization, society our daily life is based on data. therefore every data is collected using measurement or inspection activity.
In industry, lots of data are measure, on that basis they make decisions for the product or process.
So, the collection of operations, procedures, gauges, equipment, software and persons used to assign number to characteristics being measured.
Similarly, the complete process is to obtaining data by measurement is called the measurement system.

Why is Measurement System Analysis Important?
Measuring system analysis is important in quality because it helps to identify the cause and eliminate source of measurement system errors.
In any industry, accurate measurements are essential for effective decision making, process control and to meet customer requirements.
So, without a good Measurement System Analysis, organizations will make wrong decisions based on incorrect data. This will leads to huge consequences for their products, services, and overall compnay reputation.
Therefore by conducting a MSA, you can have a good understanding of the measurement variation within your processes.
This analysis allows you to differentiate between the variation caused by the measurement system and the variation due to process. With this outcome, you can make good decisions on how to improve your measurement processes, reduce variation, and enhance the overall quality of your products.
What is Measurement System Analysis (MSA)?
Now you know, if our measurement system has an error, then we get the incorrect data. Therefore the decision taken based on wrong data will result in the failure of the process or product.
So, by using statistical study and experiments conducted, we analyze the variation present in the result of inspection, measurement & test equipment system.
Hence the Measurement System Analysis is defined as the method of determination of variation in the process due to measurement system.
For the reason, the measurement system analysis (MSA) is a core element in Production Part Approval Process (PPAP).
The Guideline says that before going for process analysis through Statistical Process Control (SPC), the Measurement system should have an acceptable level of variation. Therefore MSA should be done before SPC.
Purpose of MSA
- To quantify the variation present in Measurement system
- Ensure the stability of measurement system
- Also initiate appropriate actions to minimize the measurement system variation contributed in total process variation.
Benefits of conducting measuring system analysis
Conducting a measuring system analysis offers many benefits for an organizations that are committed to produce good quality products.
- Firstly, it helps ensure accurate and reliable measurements. When a measurement system is reliable, you can trust the measurement data and you will confidently analyze and interpret the results.
- Secondly, measuring system analysis helps identify and eliminate sources of measurement error.
- Furthermore, conducting a measuring system analysis can help organizations meet industry standards and regulatory requirements. Many industries have specific guidelines and standards for measurement processes, and compliance is essential for maintaining certifications and ensuring customer satisfaction.
- By conducting regular measuring system analysis, you can demonstrate to quality assurance and ensure compliance with quality standards.
Source of variation in MSA
The source of variation in measurement system is due to the following:
- Man – The appraiser/Operator
- Machine – The measuring device, Gauges, instrument, software etc.
- Material – The object/Part being measure
- Method – Method of test, use of gauge, sample preparation etc.
- Environment – Temperature, Light’s Lux level etc.
So the total variation consist of 5 types
- Process related –
- Part To part Variation
- Within Part Variation
- Measurement system related
- Equipment Variation
- Appraiser variation
- Variation due to interaction
Key components of a Measurement System Analysis | System Errors
When you will evaluate your measurement system, you should considered below errors for the accuracy and reliability of your measurment system.
So the measurement system errors can be classified into two categories
1. Accuracy (Location Variation) – It is described as the difference between the measured value and actual / reference value also known as bias.
2. Precision (Width variation) – It is described as the variation in the inspection due to measurement system error also known as measurement variation.


What are the errors to be understand & categories for MSA studies?
1. Bias – Difference between measured value & actual value so called bias.
2. Linearity – Difference in Bias over the expected operating range of gage.
3. Stability – Difference in Bias over the extended time period hence called as stability (Time period is days- Stable over time period Uses).
4. Repeatability – It is the variation in obtained while measuring a given characteristic repeatedly on the same part
- With one measuring instrument
- By one appraiser
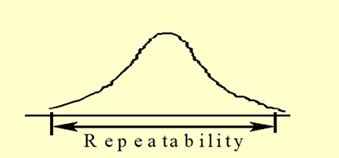
5. Reproducibility – finally It is the variation in the average of the measurement system made
- By different appraisers
- Using the same measuring instrument
- On identical characteristic of the same part

Types of Measurement System Analysis (MSA) studies / Methods

1. Bias Study
Bias is the deviation of the average observed average of measurement from the true value.


2. Linearity Study
The difference between the bias over the expected operating range of instrument is known as the linearity. “Does your gauge have the same bias over the entire operating range?”

3. Stability
The change in bias over the extended time period is called stability. Therefore the total variation observed with measurement system on the same master part, over an extended time period.

4. Gage Repeatability & Reproduciblity Study
Gauge R & R gives the combine variation of repeatability & reproducibility. This study conducted by two methods,
- Range Method
- Average and Range Method
learn more in detail about Gage Repeatability & Reproducibility (Gage R&R).

5. Attribute Measurement study
Finally, the Attribute characteristics are those characteristics where measurement values is one of a finite number of characteristics or we are not getting any measurement values. the most common example of the attribute measurement system is a go / No go gauge or visual inspection.
learn more in detail about Attribute Measurement Analysis study.
Step-by-step guide to conducting a Measurement System Analysis
Till now we have learned the important concept and benefits of MSA.
let’s dive into a step-by-step guide to run a MSA analysis for your measurement system.
Step 1: Choosing the correct measurement instrument and method
The first step in doing a measuring system analysis is to have a right measurement instrument and methods.
The instrument will be appropriate for the type of measurement, calibrated and maintained properly.
While selecting instrument, consider elements such as accuracy, precision, and stability. Select instrument that fulfill industry standards and regulatory requirements.
Step 2: Collecting and analyzing measurement data
Now you have a appropriate measurement instrument.
This step involves performing a measurements and recording the results.
You must follow standardized procedures and methods to minimize the variations from your measurement.
Use proper sampling methods and ensure that measurements are performed under same conditions.
Once you have collected the measurement data, it is time to analyze the results.
Use statistical techniques such as analysis of variance (ANOVA) or gauge repeatability and reproducibility (GR&R) to assess the accuracy, precision, bias, linearity, and stability of your measurement system.
These techniques will provide you the valuable understandings and performance of your measurement system and help to identify areas for improvement.
Step 3: Interpreting the results of a measuring system analysis
After analyzing the measurement data, it is essential to interpret the results and have a meaningful conclusions.
Look for patterns, trends, and outliers in the data to identify origins of measurement error and variation.
Interpreting the results of a measuring system analysis needs a combination of statistical analysis and practical knowledge of your measurement processes.
Step 4: Implementing improvements based on the analysis
The final step in conducting a measuring system analysis is to do improvements based on the analysis and interpretation of the results.
This involves addressing the cause of measurement error, bias, or variability that have been identified during the analysis.
Implementing improvements may involve various actions, such as
- recalibrating measurement tools
- training operators on proper measurement techniques, or
- modifying measurement processes to reduce sources of variability.
It is important to develop an action plan or necessary steps, responsibilities, and timelines for implementing these improvements.
Pre-conditions while performing MSA study
- Data should be measure under routine measurement conditions.
- Basic control should be exists, so that it used without required measurement system analysis.
- Equipment should be calibrate
- Adequate discrimination
- Persons are qualified
- Un-necessary causes of variations do not exist etc.
Measurement System Analysis
MSA condusted before the SPC. Also when we use new gage/instrument for inspection, calibrate and do the MSA of that gage bfore use cases.
1. Gage/instrument/measuring equipement
2. Operator/inspector/personal
3. Parts/standard gage/product
MSA perform to check our measurement system is capable or not.
Is there any variation present in our measruemet system or not.
Measurement System Analysis standard manual created by AIAG (Automotive Industry Action Group).
Current revision of standard is “Measurement Systems Analysis (MSA), 4th Edition, June 2010”.

I am a full time Engineer and Quality Professional with over 11+ years of experience in the automotive industry. My professional journey has started from a small enterprise quality inspector to a advanced quality expert. I am creating a good-quality content for engineers. Help them to grow in their career.Learn more here.