First Part Inspection (FPI) is one of the quality control process in manufacturing. It means the inspection of first part produced by a manufacturing process.
Therefore the first piece is confirm that remaining parts will produce as per required specification.
The method is done by comparing the dimension of first part with the control plan or drawings or 3D model design. This process is looking for the defect or any deviation on the product from the actual specification requirement.
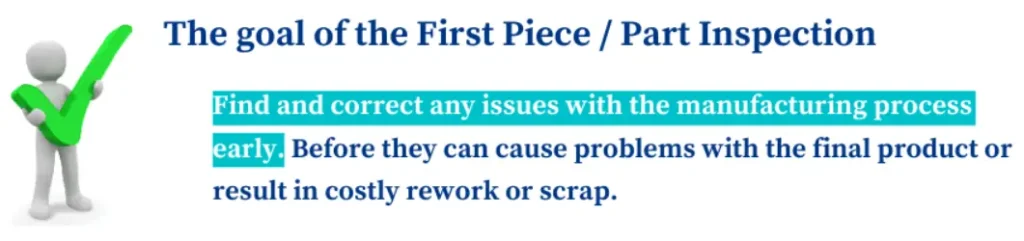
The purpose of First Piece/Part Inspection is to identify and correct any defect/issues with the manufacturing process before start of production.
Before they can cause problems with the final product or may result as costly rework or scrap.
Many companies have different names for first part inspection as Ok 1st part, First piece inspection, first off par, first part approval, first piece approval, first article inspection, first-off part validation, etc.

Why we do the first part inspection?
Our manufacturing process needs to ensure that, the final product meets all customer specifications and tolerances.
Therefore, the first part inspection is done to ensure that the manufacturing process is operating properly and final products will be of high quality.
First part inspection is an important step in the manufacturing process, it helps to identify and correct any potential problems before they affect the entire production run.
This can save time and money by preventing the need for rework or scrap, and it can also help to improve the overall quality of the final products.
ISO 9001:2015 requirement for the first part inspection

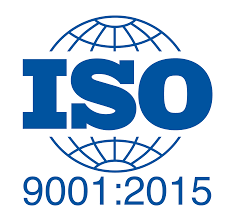
ISO 9001 is a standard for quality management systems. It does specifically mention the requirement of “Control of production and service Provision”.
However, it does include a clause (8.5.1) that requires the availability of documented information that defines the product characteristics to be produced or activities to be performed, and results to be achieved.
IATF 16949:2016 requirement for first part inspection


IATF 16949 is a standard for Automotive quality management systems. It does specifically mention the requirement of “Control of production and service Provision”.
However, it does include a clause (8.5.1.3 – Verification of job setup) that requires performing first-off / last-off part validation.
When first part inspection is required?

First part inspection is needed
- Before the start of the shift
- Change in material
- Tool / Machine setup change
- Operator change
- The new product is being introduced to the market, or when a
- The product is being manufactured according to a customer’s specific requirements.
- Manufacturing process is being modified or changed in some way. For example, if a company is implementing a other / new manufacturing technique or using different materials, a first part inspection may be necessary in order to ensure that the process is operating correctly and producing high-quality products. [/read]
How to do first part inspection?
There are several steps involved in conducting a first part check.
These steps may vary depending on the specific product being inspected and the manufacturing processes used.
But in general, the process typically includes the following steps:
1. Identify the process, product and its specifications: Drawing’s
Before beginning the inspection, it is important to identify the product and process characteristics and review its specifications and tolerances.

This will help to ensure that the inspection is conducted correctly and that the final product meets all of the necessary requirements.
2. Gather the necessary tools and equipment:
In order to conduct the inspection, you will need to have the right tools and measuring equipment on hand.
This may include calipers, micrometers, gauges, and other precision measuring tools, as well as a checklist or other documentation to help guide the inspection process.
3. Inspect the product and process:
Once you have all of the necessary tools and equipment ready, you can begin the inspection process.
Start by carefully checking the product and process. Use the appropriate tools and techniques to measure and evaluate product and process key features and dimensions.
Be sure to pay close attention to any areas of the product that are critical to its function or performance, as well as any areas that are prone to deviation or defects or errors.
Inspection and testing procedure are important to deal with such requirement.
4. Document the results: First Part Inspection Report
As you conduct the inspection, be sure to carefully document the results of each measurement and evaluation. Use first part inspection report to document the record.
You can download first part inspection report below,
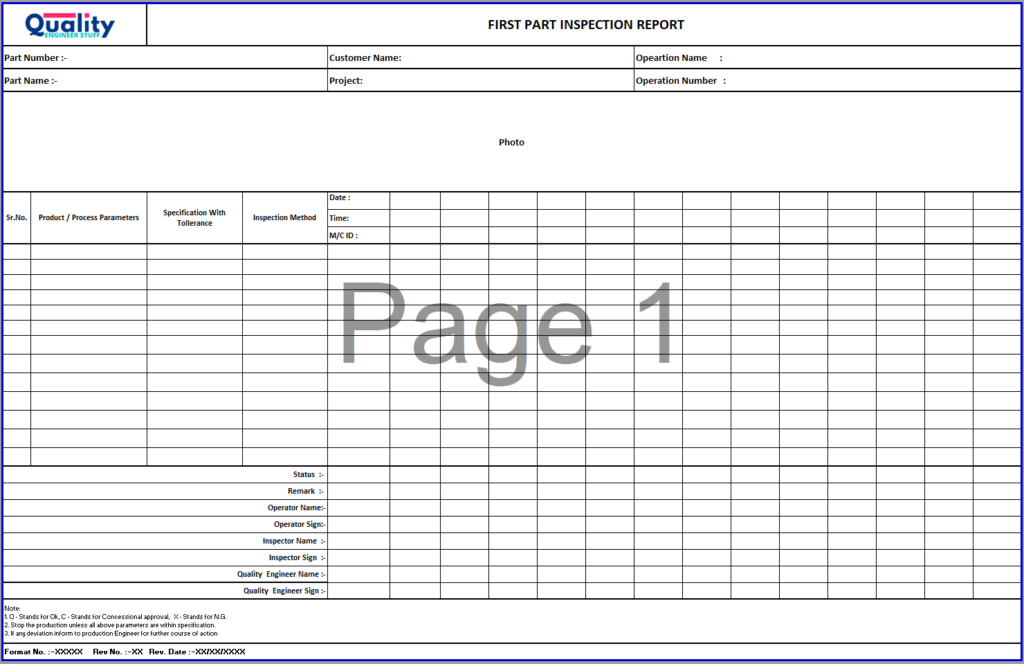
This will help to ensure that the inspection is thorough and complete, and it will provide a record of the product’s quality for future reference.
5. Compare the results to the specifications:
Once the inspection is complete, compare the results to the product and process specifications and tolerances.
If the product meets all of the necessary requirements, it can be approved for use in the manufacturing process.
And if there are any issues or concerns, they can be addressed and corrected before start of production. Sometimes deviations need to sign and approved to start production before correction.
first part inspection sample size

The sample size for the first part checking will depend on a number of factors, including
- the complexity of the product,
- the number of dimensions or features that need to be inspected,
- overall quality requirements for the product.
In general, the sample size for a first part check should be large enough to provide a representative sample of the product. But not so large that the inspection becomes excessively time-consuming or costly.
As a general rule, a sample size of 5-10 units is often sufficient for a first part check.
In some cases, a larger sample size may be necessary if the product is particularly complex or if there are a large number of dimensions or features that need to be inspected.
It is important to remember that the sample size for a first part check is not set as a thumb rule. So, it can be adjusted depending on the specific circumstances of the inspection.
Advantages of the First Part Inspection
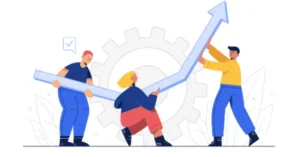
There are several advantages to performing a first-part inspection in manufacturing. Some of the most important benefits include:
- Ensuring that the parts produced meet the required specifications and tolerances, which is critical for the performance and reliability of the final product.
- Identifying and correcting any issues with the manufacturing process early on, before they can cause problems with the final product or result in costly rework or scrap.
- Providing documentation that can be used to demonstrate compliance with industry standards and customer requirements.
- Providing valuable feedback that can be used to improve the manufacturing process and reduce the likelihood of defects or other issues in the future.
- Helping to build confidence in the quality of the parts being produced, which can improve customer satisfaction and reduce the risk of returns or warranty claims.
Conclusion
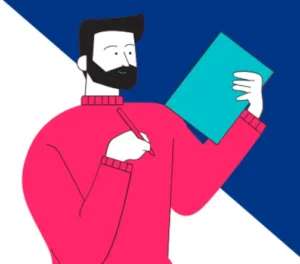
Overall, the first article inspection is an important quality control step. That can help manufacturers produce high-quality parts and improve their manufacturing processes.