In this article, I’m going to explain to you a complete guide about 5 quality core tools.
I probably don’t need to tell you that you have a good potential to learn the quality concept and improve your skills in the organization.
And here you will learn these core tools in a good, organized way.

Learning these tools will enhance your knowledge and skills as a Quality / Industrial Engineer. Just go through the articles you will be in flow to know the importance of these core tools.
Let’s dive right in…
Why Core Tools? | Importance of Quality Core Tools
In the competitive market, First Time Right Product is the key to success in business.
You can see the core tool assessment survey published by AIAG..
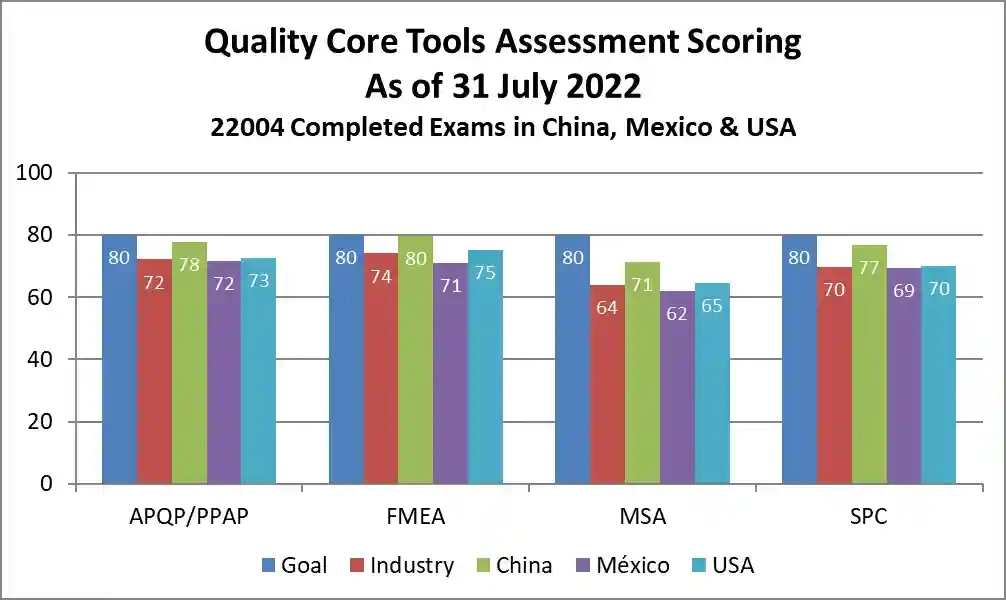
How to achieve First Time Right product requirement?
So, to achieve the First Time Right product, we need some standards and tools such as Quality core tools to use in the development process.
Once we align with core tools, we can develop the best-in-class product in our category. The core tools will help us throughout the product development process to manufacture First Time Right and Best in Class products and services.
Also, the core tools play important role in the Quality Management System. The baseline foundation of the Quality Management system is the Quality Core tools.
Let’s dive into the core tools list in detail…
What are the 05 Quality Core Tools?
The 5 core tools are the sequential tools and methodologies used in Product Development Cycle and Manufacturing processes. These tools are mandate by the IATF 16949 standard.
Below is the list of 05 core tools

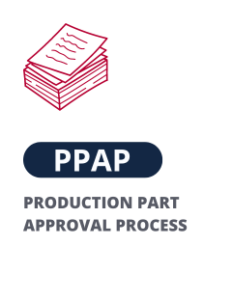
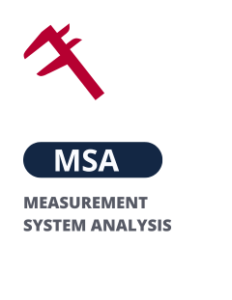


These 5 quality core tools and methodologies have been developed and published as Manuals by the Automotive Industry Action Group (AIAG).
#1 APQP (Advance Product Quality Planning)

APQP is an important tool in Product Development Management. This tool will help you to follow the complete roadmap of the development process.
You may think why we need the APQP for more specifics. Our primary goal is to meet the customer requirement. To know what exactly the customer wants. So to fulfill the customer’s wants, there is a specific way to capture the requirement and fulfill the same.
How does the APQP tool perform?
Now there are 5 stages in the Advance Product Quality Planning process. In the development process, these stages are also known as Phases or Gates.
Each Phase requires some inputs and we will get the output once the phase or Gate is completed. The output of the previous phase is the input for the next phase.
It is the Master process and the other tools are also an integral part of APQP.
#2 PPAP (Production Part Approval Process)
PPAP is the primary requirement from the customer in the industry. It is considered the standard which includes the set of documents.

The PPAP is the customer approval process. Once your PPAP is approved by the customer, it means that the supplier production process is capable to meet all customer requirements.
This is the agreement with all documents between customers and suppliers, where supplier understand all the customer design and requirements. Also, the supplier Production process is capable to produce the parts at the required run rate.
Based on the PPAP guideline by AIAG, there are 05 levels of approvals from customers. Therefore it depends on customer, and which level of PPAP they want from the supplier.

The complete Production Part Approval Process includes 18-20 Different types of documents. Finally, it depends on the customer which documents set they need for the approval process.
#3 FMEA (Failure Mode and Effect Analysis)
Many manufacturers are facing high product recall / huge fines due to product failure. So, the Failure Mode and Effect Analysis tool is the best methodology to capture these failures during the initial stage of development.

The FMEA method is widely used in industry. The core purpose of the FMEA is risk analysis in the initial design stage. Therefore it is also known as failure prevention methodology.
How does FMEA reduce risk?
The FMEA is the Form that needs to be filled by the cross-functional team (CFT) or multi-disciplinary team (MDT) using the brainstorming method.
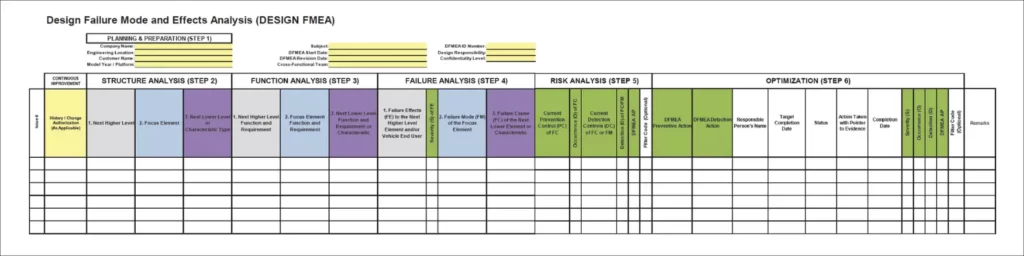

The method has the criteria to prioritize the risk based on the Risk level. And the risk level is calculate on the basis of Severity(S), Occurrence(O), and Detection(D) level combinations.
#4 MSA (Measurement System Analysis)
Generally, we take decisions based on the data, and how exactly we are sure the data is correct or not.
In the industry, a massive amount of data is recorded using measurement and inspection. For accurate data, we should make sure that our measurement system is good enough.
To check the measurement system’s effectiveness we do the Measurement System Analysis (MSA). We must know how much error is present in our measurement system. Therefore it is advisable to do MSA before doing measurement or inspection of parts.

The measurement system includes parameters such as Operator, Measurement equipment, Parts, Environment, methods, standards, etc.
#5 SPC (Statistical Process Control)
What do you exactly know about SPC? This is the statistical method to measure and control the production process.
We generally collect data from the manufacturing line using measurement and inspection and based on the data we will accept or reject the part.
But this is the method of acceptance and rejection of parts only.

When you look at the long-term process, then the statistical data is been analyzed using statistical tools and predict the manufacturing process that is capable or not when the process will out of specification.
The statistical Process control is the continuous improvement method.
Core tools requirement clauses in ISO/IATF 16949:2015 standard
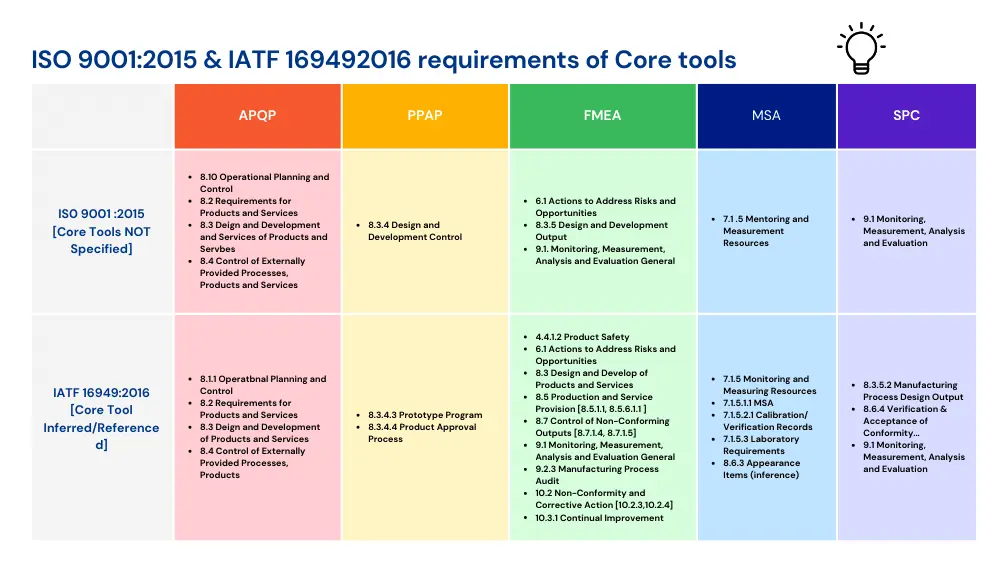
Quality core tools | What did you learn here?
I hope you go through the What is core tools? and an overview of the 5 core tools of quality. And the importance of the core tools.
The core tools are the foundation of effective Quality Management System, also it is incorporated in ISO/IATF 16949:2016.
It is not possible to explain all five tools in a single article, so please look into respective articles in detail with examples and case studies.