This is a complete guide to learn about APQP.
If you really want to learn the detailed APQP process in an easy way, you will enjoy and learn in this post.
Therefore, the purpose of this post is to get the concept knowledge of the APQP process.
Let’s start in…


What is APQP?
APQP (Advance Product Quality Planning) methodology is developed by AIAG (Automotive Industry Action Group).
Therefore it is a systematic way of tracking, defining, and planning the development steps.
These steps are present in the product and process development phase to satisfy the customer (Internal & External).
Therefore this process captures the voice of the customer (VoC) to satisfy the customer.
APQP is the automotive core tool and applies during the product & process development phase.
Why is APQP so important?
Back in the day’s, there are many challenges in the automotive industry
- Innovation
- More complex Product
- Reduce new product development time
- Complicated supply chain activity
- Increase in customer and quality requirement

To overcome these challenges, we have a solution. The automotive industry adopted this APQP process.
APQP method is used to achieve similar benefits. such as
- Avoid late changes in Product and process.
- First-time right-quality product
- Low cost
- Reduce risk at an early stage
How to Implement APQP process?

Specifically, the Advance Product Quality Planning (APQP) cycle works as per PDCA methods.
Therefore the APQP process consists of Five phases & Four major activities.
Also, it has 20+ supporting tools along with ongoing feedback and action plans.
Similarly, the supporting tools include DFMEA, PFMEA, CTQ, Special Characteristics, Control Plan, SPC, etc…
Fundamentals of APQP
Before we go for the phases in APQP,
It’s important to focus on the fundamentals required to complete the APQP process.
With that, Here are the fundamentals of APQP process that is used before starting..

APQP fundamentals
The management should assign the responsible person for the APQP process. Also to form a cross-functional team for effective planning.
The team should include persons from various departments in the organization.
Such as Marketing, Engineering, Quality, Purchasing, Packaging, Customer representative, etc.
Each function such as product development needs a Product design team.
And process development needs process manufacturing experts in CFT.
However, the project scope is also important initially. So that the scope includes the customer voice, roles and responsibilities, and quality, cost, and delivery impact.
Finally, the APQP process is start with the product quality plan.
Therefore the CFT will review the product concept, past experience, and milestones. So that they can make a product quality plan to satisfy the customer.
As a result, the product quality planning team focus on defect prevention to meet customer expectation.
So to achieve the quality plan, it is linked with product timing plan to complete the APQP process within a timeline.

Phases in APQP process
Its no secret that APQP is the key to product development
As it turns out the process is completed in phases
So, here are in the diagram shows five types of phases, which undergoes the APQP process.
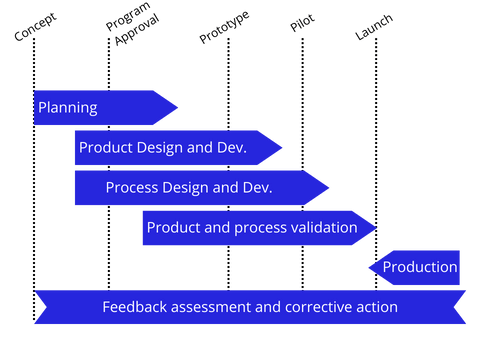
There are five phases of APQP
- Planning
- Product design & development
- Process design and development
- Product and Process validation
- Production / Feedback assessment and corrective action
Phase #1 – Planning
The objectives of the plan and define phase are To determine customer needs and To plan a Quality Program.
Therefore in this phase #1 the voice of customer should be clearly defined and understood by team members.
There are inputs required for each phase. And you will get some output of the respective phases.
Let’s see what are the input require in the planning phase and similar outputs of that phase?
Input
- Voice of the Customer
- Market Research
- Historical Warranty and Quality Information
- Team Experience
- Business Plan/Marketing Strategy
- Product / Process Benchmark Data
- Product/Process Assumptions
- Product Reliability Studies
- Customer Inputs
Output
- Design Goals
- Reliability & Quality goals
- Preliminary Bill of Materials
- Product Assurance Plan
- Preliminary Process Flow Chart
- Management Support
- Preliminary list of Special Product and Process Characteristics
Phase #2 – Product design & development
The objectives of the Product design & development phase are To develop design features and characteristics.
Also critically review engineering requirements, and finally assess potential manufacturing problems.
Therefore in this phase #2 development of the design into near final form is to be done.
And prototype, feasibility, volume study, and manufacturing schedules are to be reviewed.
Let’s see what are the input require in Product Design and Development and similar output of that phase?
Output of phase#1 is input for phase#2
The output of Phase#2 Product Design and Development are,
- Design FMEA (DFMEA)
- Manufacturing and Assembly Design (DFM/A)
- Design Verification
- Prototype Control Plan
- Engineering Drawings CAD the Master
- Material Specifications
- Design Review
- Engineering Specifications
- Change Control for Drawings
- New Equipment, Tooling, and Facilities Requirements
- Special Product and Process Characteristics
- Gages / Testing Equipment Requirements
- Team Feasibility Commitment and Gateway approval
Phase #3 – Process design and development
The objectives of the Process design and development phase are To develop a comprehensive and effective manufacturing system.
Also to ensure that the manufacturing systems meet customer requirements.
Therefore in this phase #3 Develop a manufacturing system and its related control plans to achieve quality products.
Let’s see what are the input require in Product Design and Development and similar output of that phase?
Output of phase#2 is input for phase#3
The output of Phase#3 Process design and development
- Packaging Standards and Specifications
- Quality System Review
- Process Flow Chart
- Floor Plan Layout
- Characteristics Matrix
- Process FMEA (PFMEA)
- Pre-Launch Control Plan
- Process Instructions
- Measurement Systems Analysis (MSA) Plan
- Preliminary Process Capability Plan
- Gateway Approval
Phase #4 – Product and Process validation
The objective of the product and process validation phase is to validate the manufacturing process.
Also to ensure that customer expectations will be met. So, to identify additional concerns.
Therefore in this phase #4 Validate the manufacturing process through a production trial run.
To validate that the control plan and process flow chart is effective and that the product meets customer expectation.
Let’s see what are the input require in Product Design and Development and similar output of that phase.
Output of phase#3 is input for phase#4
So the outputs are
The output of Phase#4 Product and Process validation
- Significant Production Run
- Production Part Approval Process (PPAP)
- MSA Results
- Process Capability Studies
- Production Validation Testing
- Packaging Evaluation
- Production Control Plan
- Quality Planning Sign-Off and Gateway Approval
Phase #5 – Feedback assessment and corrective action
The objective of the Feedback assessment and corrective action phase is To evaluate the output of the APQP phases.
Therefore in this step, the effectiveness of the product quality planning efforts is being assessed.
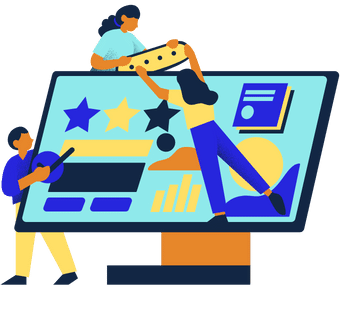
Let’s see what input require in feedback assessment and corrective action and similar output of that phase.
Output of phase#4 is input for phase#5
Output of feedback assessment and corrective action phase
- Reduced Variation.
- Improved Customer Satisfaction
- Effective Use of Lessons Learned
- Improved Delivery Performance
Summary of APQP (Advance Product Quality Planning)
Finally here is the quick list of summaries, I’ve picked up in this APQP process…
So that you can summarize the documents and purpose of APQP.

What we do:
- Design Quality
- DFMEA / PFMEA
- Manufacturing Quality
- Process Flow
- PFMEA
- Control Plan
- Measurement System Analysis
- Capability Analysis (SPC)
- Process Validation
- Run at rate
- Supplier Qualification & Quality Requirements
- Product Qualification
- PPAP
- 1st Article Inspection
- Tooling & Gauges
- Testing
How do we do it?
We do all the processes by upfront detailed quality planning.
What do we get?
- Defect Free Launches
- Reduced Warranty Claims
- Zero Spills
- Customer Satisfaction
- Robust Products
- Greater Supplier Control
- Reduced Supplier Cost
Benefits of APQP (Advance Product Quality Planning)
Now it’s time for me to show you the benefits of the APQP process.
You will not read this before…

Finally during the development manufacturing process functions are clearly planned.
So it will validate, document, and communicate the results in the:
- Robust and reliable designs
- Reduced process variation
- Enhanced confidence in supplier’s capabilities
- Better-controlled process changes
- Defect free launches
- Improved Customer satisfaction
- Maximum ROI
- Improved Delivery and Service
- Minimum Waste
- Minimum Cost of Non-conformance
This is a complete guide to learn about APQP. As this is one of the Quality core tools. You can learn other core tools.

I am a full time Engineer and Quality Professional with over 11+ years of experience in the automotive industry. My professional journey has started from a small enterprise quality inspector to a advanced quality expert. I am creating a good-quality content for engineers. Help them to grow in their career.Learn more here.