PPAP is the key process in manufacturing industry. At last it is a gateway to start the manufacturing after getting approval from customer.
Basically every quality engineer interview starts with the topics like APQP and PPAP documentations.
Many quality professionals are struggle to understand the concpet and due to fear of dcumentation they are facing failure.
But this PPAP guide will explain you the complete PPAP process and the basic to advanced understanding behind.
Let’s go through the detailed articles line by line.
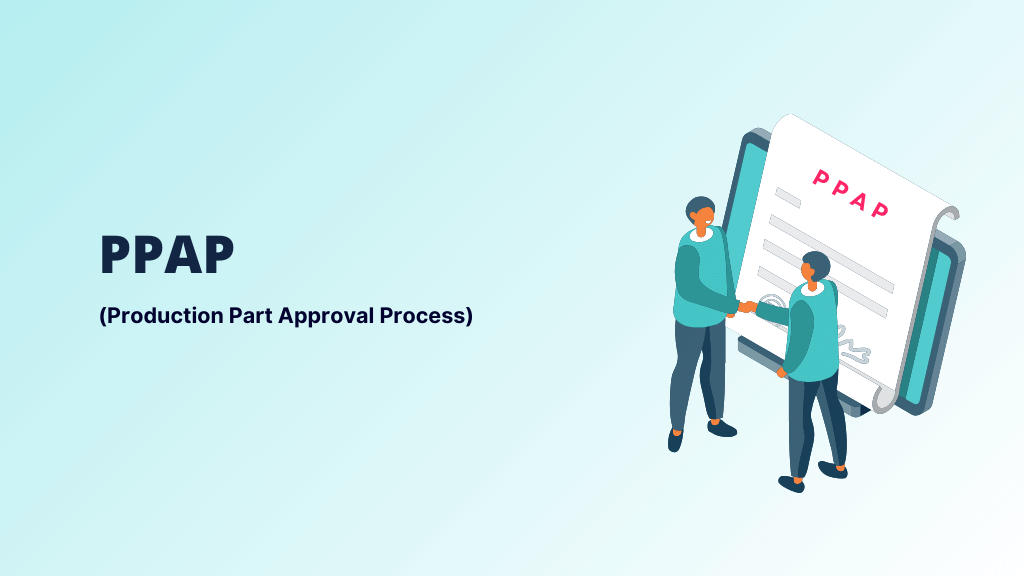
What is PPAP?
Full form of PPAP is “Production Part Approval Process”. PPAP includes total 18 No’s documents, which helps to get approval of production run from the customer.
These Documents used to reduce risks before product release, with help of team and by using established tools and techniques.
PPAP is developed by “AIAG” (Auto Industry Action Group) in 1993, by 3 companies GM, Ford & Chrysler. Now a days, PPAP is spread to many different industries which are beyond automotive.
Why PPAP? What is purpose of PPAP?
The purpose of PPAP is to submit the evidences that the supplier understand all customer engineering design specification and their requirements to produce the parts consistently meeting all requirement during actual production run at given production rate.
This is the brief definition. But for common understanding, we do the new deveopement of product.
The development cycle starts from the planning to product design the process design, Product and process validation and then final production launch.
Now, PPAP is required at the production launch stage. Where all required documents are been check by organization or customer. And then based on the evidence customer will provide the approval.
This approval consist of many documents, and those documents we called as PPAP documents. This will be complete one file containing all evidences of the initial development.
When PPAP is done?
- New Part Development
- Changes In
- Engineering release
- Processes flow (New / additional machines)
- Process
- Layout
- Raw material ( Equivalent / Alternate)
- Manufacturing location
- Sub supplier / location
- Die/Tool (Major modification / New / additional / Inactive more than 12 months
PPAP Submission Level
During PPAP process there is 5 level for submit the PPAP.
- Level 1 submission – Part Submission Warrant (PSW) submitted to customer.
- Level 2 submission – PSW, product samples, and dimensional results submitted to customer.
- Level 3 submission – PSW, product samples, and complete supporting data submitted to customer.
- Level 4 submission – PSW and other requirements as defined by customer.
- Level 5 submission – PSW, product samples and complete supporting data (a review will be conducted at the supplier’s manufacturing location)
PPAP requirements / 18 Documents of PPAP
There is 18 documents / elements used in PPAP requirement,
1. Design Record – All design records for the salable product e.g. Part drawings (Ensure Engineering Change Level is Latest), Material Specifications, Engineering Specification Standards.
2. Engineering Change documents – If there is change in part which is not in drawing then there is change approval documentation is mandatory. The change is documented
3. Customer Engineering Approval – Further if specified by the customer, the supplier has the evidence of customer engineering approval.
4. Design Failure Mode and Effects Analysis (D FMEA) – In many cases there is customer design, in that case D FMEA is not applicable. But if the supplier is design responsible then it is required.
5. Process Flow Diagram – It shows the flow of the product from incoming raw material to the final product.
6. Process Failure Mode and Effects Analysis (P FMEA) – PFMEA is live document, in which we identify all failure modes, their potential causes and then apply the respective controls on it.
7. Control Plan – Control plan is the output of PFMEA, which includes the controls on both product and process characteristics to maintain the product quality consistently.
8. Measurement System Analysis Studies – MSA includes the study on all dimensional measuring instruments to validate that the measurement system is good for product quality inspection. It consist of the Gage R&R and other studies depends on the type of data, such as Attribute MSA for attribute data.
9. Dimensional Results – It includes your measurement such as tooling installation reports, samples inspection reports, Layout inspection reports, CMM records etc.
10. Records of Material / Performance Test – It includes the Raw Material test certificates, Surface treatment test certificates, design validation reports etc.
11. Initial Process Studies: It is the acceptable process capability of the special characteristics for initial production samples. So, this will give us an idea of how capable you are to produce ok parts consistently and there is need to submit Statistical Process Study report as a PPAP document.
12. Qualified Laboratory Documentation – Generally it should includes the material test done by external lab NABL (National Accreditation Board for Testing and Calibration Laboratories) records, ELV (End of Life Vehicle) reports, Chemical & mechanical properties test reports etc.
13. Appearance Approval Report (AAR) – In fact it applicable for aesthetic characteristics, in which customer inspect the final product & approval by giving aesthetic sign-off.
14. Sample Production Parts – PPAP lot quantity define by customer, Confirm and Agree the PPAP Qty in the Initial stage itself. Make documents for sample parts submitted.
15. Master Sample – Master sample is the part on which internal & customer sign-off available although there is need to retain this part with sign-off sheet documentation.
16. Checking Aids – This includes the list of all measuring resources used in production. This is tools, Instruments, gauges, fixtures, checking panels etc. This needs MSA also for all checking aids as required by customer.
17. Customer-Specific Requirements – This document contains other special customer requirements. For example the bulk materials, applicable customer-specific requirements to documented on the bulk material Requirements Checklist.
18. Part Submission Warrant (PSW) – Finally after completion of PPAP process, the supplier should submit the Part submission warrant (PSW) to customer. All PPAP summary is included in PSW.
One more additional document is there but this is applicable when you are responsible for bulk material manufacturer.
19. Bulk Material Checklist: This is applicable when you are manufacturing and supplying the bulk material. It is completely depends on the customer. If customer wants to have the bulk material checklist for PPAP then you need to produce this.
Benefits of PPAP
- Ensures formal quality planning
- Helps to maintain design integrity
- Identifies issues early for resolution
- Reduces warranty charges and prevents costs because of poor quality
- Assists with managing supplier changes
- Prevents use of unapproved and nonconforming parts
- Identifies suppliers that need more development
- Improves the overall quality of the product & customer satisfaction