Every managers and quality executive need this tool and technique, therefore it is must to know how to calculate the cost of quality in the organization.
It is not just because the management is ask for the result of quality department. But you must take action to improve the organization condition.
So the cost of quality and cost of poor quality is essential method in all aspect of quality.
Managers and workers speak the language of things but Senior leaders speak the language of money…
According to the above quote.
We can say that, the cost of quality calculation allows us to convert the things into money.
Also we will see case study on quality cost and how it is effective methodology.

History of cost of quality (COQ)
It was Joseph Juran first discussed the cost of quality analysis. This was discussed in 1951 in “Quality Control Handbook”.
Again in 1956, It was Armand Feigenbaum Who identify four quality cost categories.
Then Total Quality Cost Committee was established in 1961 by ASQC.
What is Cost of Quality?
There are many definitions of cost of quality. Among those we can prefer simple one.
The cost which use to attain the quality, this cost is align with the product quality called as cost of quality.
Therefore the cost of quality is the methods use to identify the resource cost.
What type of organization resources are use to maintain the product quality.
This includes the cost of internal and external failures.
Therefore the cost of quality is the sum of cost of Good quality & cost of poor quality.
Why do we need to know
Cost of Quality?
Importance of the Cost of Quality tool is, It speaks the language of management. This tool speaks the language of money.
Now a days, the business environment is more competitive. Lot of options are available with customer. So company should able to produce the product with low cost to survive.
Therefore in the industry the top companies are surviving good. This is just because they produce the product as per voice of customer with high quality.
Such companies are use cost of quality to analyze and take actions to grow there profit.
Researches shows that the organization have the cost of poor quality ranges from 15% to 40% of the business cost.
Its the huge cost for any organization. Therefore this tool helps to identify those costs.
Money is the language of management, you need to show them the numbers…
Crosby
Producing non confirming products will lead to warranty failures and will effect product recalls.
This will be the major impact on organization. Therefore the cost of quality will help us to identify those impact.
So it can prioritize quality improvement actions. This cost data shows us how our profit is affect by quality.
Goal of COQ system
Now the goal of cost of quality system is to increase the prevention in the process. This will help to eliminate external and internal failure cost and reduce the appraisal intervention and respective cost.
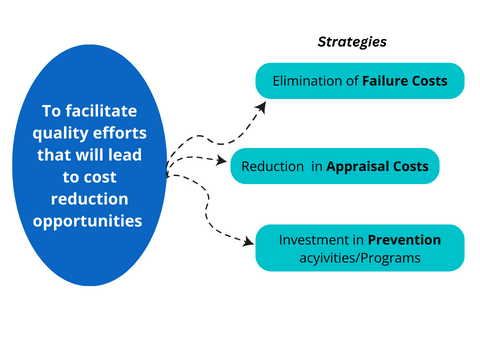
Let’s learn all this types of cost categories in detail,
Categories of Cost of Quality
You must know how the cost of quality categorize.
As you need to calculate the cost of each category. so this will help you to find out the exact cost for each category.
The cost of quality is primarily categories in two way. refer the below chart for clear understanding.

Cost of Quality Vs Cost of poor Quality
Cost of Good Quality
It is the cost to achieving the good quality.
This cost is incurred in ensuring that things are done right the first time.
It is the cost for supply product or service as per standard.
We can say this is the good amount spent.
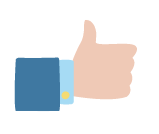
Cost of Poor Quality
It is the cost incurred by the company due to poor quality products produced.
This cost is incurred as a result, not doing things / steps right the first time.
We can say this is termed as unnecessary amount spend.
It is the failure cost by operating process not as per standard.
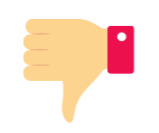
Now lets have look, to learn each category of cost,
What is Prevention cost
Prevention cost is to prevent the defect / failure from happening.
This cost associated with design, implementation, maintenance & planning. Therefore this is applied prior to actual production.
Prevention cost will help us to minimize the appraisal and failure costs.
Therefore this cost is design to prevent production of poor quality products.
Examples of prevention cost:
- New product review
- Quality planning
- Process capability studies
- Quality improvement
- Quality Audits
- Team meeting & Projects
- Quality education and training
- Market survey
- Customer survey
- Design review
Prevention cost will be the largest proportion of total cost of quality.
Intellectuals solves problem,
Albert Einstein
Geniuses prevent them…
What is Appraisal Cost?
So the appraisal cost are spent to detect the defects / failures.
In the field of manufacturing process or service we are using the personals to check the product for defect. This is done to give assurance to conformance of quality standards.
Typically this cost spends on inspection and testing. also some means of measurement system analysis.
If our product is conformance to standard then this cost is for cost of quality.
And if we are spending appraisal cost for non confirming product, then this cost will belongs to cost of poor quality.
Therefore appraisal cost is mainly focus on discovering the defects rather than prevent it.
Appraisal cost is the second largest cost, but should not exceeds the prevention cost.
Examples of appraisal cost:
- Inspection of test / purchase material
- Internal audits
- Calibration cost
- Calibration of measuring and test equipment
- Non destructive testing cost
- Product audit
- Process audit
- Internal Quality audit
- Inspection cost
What is Internal failure cost
This is the failure cost for the products in manufacturing plant.
This cost is due to failure / defect cost before shipment to customer.
We can eliminate this cost y producing zero defect product. And this is the major challenges in manufacturing industry.
This will be achieve by Statistical process control technique or six sigma technique.
Examples of internal failure cost:
- Cost of scrap, defects, rework etc.
- Re-inspection cost, re-test to verify the performance of the system.
- Downtime
- Production loss due to unavailability of material (Inventory)
- 100% inspection cost.
What is External failure cost?
This cost will impact most to the organization. Because this cost is incurred after dispatch of the product to the customer.
As we see this cost will occur at customer end, in the form of customer complaint and rejection, warranty failure etc. Therefore it will leads to customer dissatisfaction as well as impact to your brand image.
So the external failure cost will hit major impact to your business.
That is the reason why this cost mitigation is more important. We should focus on eliminating the external failure cost.
Examples of external failure cost:
- Warranty failure charges
- Customer complain resolution: This will include the customer complaint analysis, Defect cost and the cost of resources use while handling customer complaint.
- Product recall
- Allowances
- Premium freight price
Cost of Poor Quality (COPQ)
The name suggests, the cost incurred to the company due to producing the bad parts are the cost of poor quality (COPQ).
That’s why we use the term cost of poor quality.
By referring the below illustration you can understand how big is COPQ impact to company.
Majority of COPQ are not easily identified and quantified.

By find out those hidden cost, company can prevent those cost by eliminating the nonconforming product.
Lets dive into important topics ahead.
Measuring Cost of Quality
The cost can be calculated or measure in many ways,
Such as in Rupees or in % of sale,
- % age of sale
- % age of profit
- % of manufacturing cost
- Rupees per unit of product
Steps include in implementing the quality cost system
- Get the knowledge on quality cost and similar industries who are using the same tools.
- Now select the area / production line or plant on which you want to implement the COQ system.
- Set the objectives with the help of key people in the organization.
- Now with the help of management and other system collect the cost data for the study.
- Now collect data by identifying each work area contribute to the cost of poor quality. Such as work records, job description, interview, flowcharts and brainstorming will help to identify those cost.
- Make a draft for the categories of cost of quality and poor quality.
- Collect and summarize data, at ideal condition this should be done by account personal.
- Present the cost result to the management and start assigning the quality improvement project to respective improvement areas.
Case study
Example on Cost of quality
Let’s see the case study of H&S motors,
H&S motors is the small company produces the motors for lawn movers and garden equipment.
The company added a quality improvement program in 1999, and has record the following quality data,
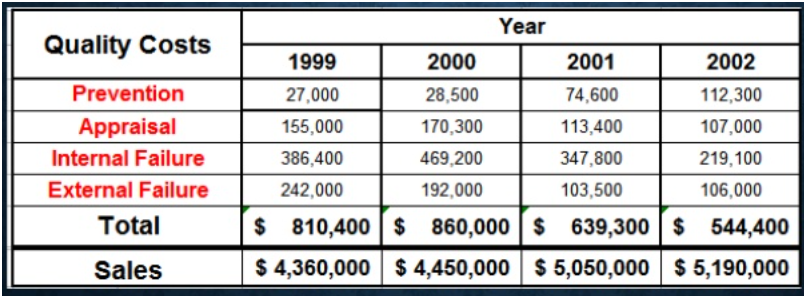
Company want to develop a program and It is the data on sales basis for the 4 year.
Key points from the above study:
Approximately 75% of total quality cost spends due to internal and external failures.
So in year 2000 company spends more money on product monitoring and inspection. Therefore this result into high appraisal cost.
Due to this strategy of spend more money on product monitoring & inspection, company was able to identify more defective items.
This will result as to increase in internal failure cost but the lowers the external failure cost.
Now in 2001 & 2002 company spent more money on prevention activities. That was training of employee, planning, improving product quality etc,
The cost of prevention in increase by 300% in last 4 years. This will leads to decrease in cost of poor quality.
The company develops the index number using quality cost,
Therefore the quality index for 1999 sales is,
=(810400 / 4360000)*100
=18.58
And refer below similar for other years,
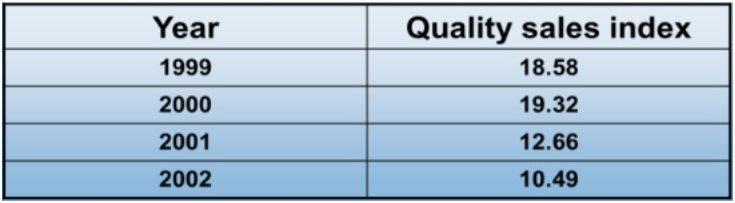
This sales index number is self explanatory. You will get, how effective is the quality cost management program for the company.
By eliminating a defective product in early stage of production, a company can reduce its cost of poor quality.
Therefore investing in prevention cost is extremely important…!
Conclusion:
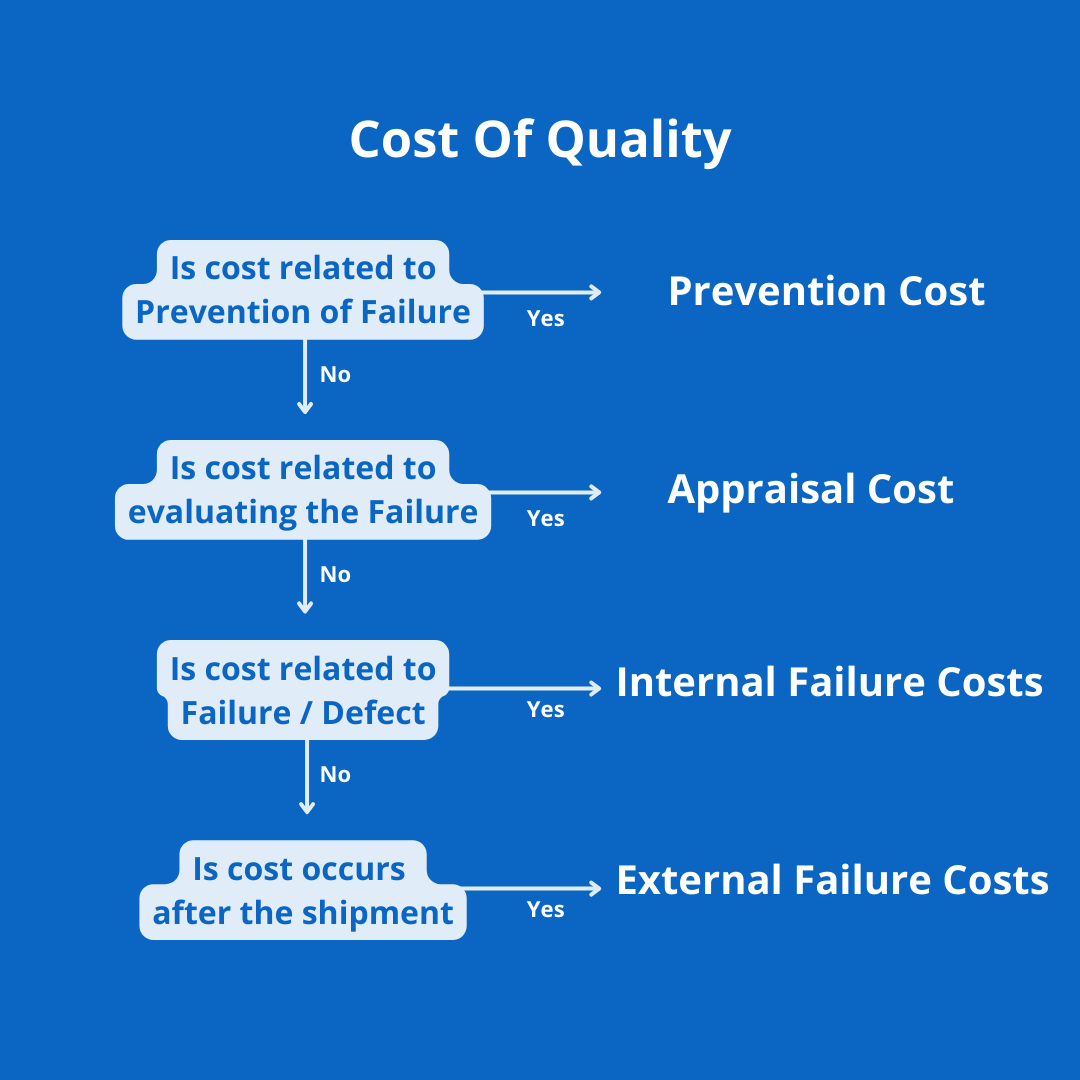
The cost of poor quality can be report in endless number of ways.
It can be the 10% of company sales, you can define you objective as per management requirement. or on base of industry benchmark.
Once you represent the quality in the language of money you will realize the true significance of cost of poor quality.
Quality cost are dynamic and constantly changing over time.