Root Cause Analysis –>Think about the major problem you faced at your work.
Did you give time to analyze the problem and try to fix it. Or you just quick fix the problem by reducing the problem symptoms.
If you only focus on reducing the symptoms of problem then the problem is still in your system.
The only way to eliminate the problem is to find out the root cause and eliminate it.
Therefore the root cause analysis is the key skill every quality engineer must have.
It will help in continuous improvement also. When you think about your complete process as SIPOC, at every stage there is scope for improvement. Then you can identify probelm definition and try to solve the problem using proble solving methods such as Root cause analysis..
Using this article you willhave complete undertsnading of root cause analysis and problem solving method.
Let’s dive in.

What is root cause analysis?
Root cause analysis tools is the structured investigation that aims to identify the causes of problem. In many cases after the fault or problem occurrence, we try to fix those problem quickly without any analysis. Therefore it will leads to re-occurrence of the problem in future.
And when the problem comes repeat in future it will affect to cost and waste in the system. In other words if problem comes repeatable, it will generate more defects in the process. It will leads to customer dissatisfaction and affects the product quality.
For systematic identification of the root causes to eliminate the problem, here we have the solution. The root cause analysis is the powerful tool to address those causes and fix the problem. This tool is applicable not only in manufacturing but also applicable in all life cycles problems.
How to perform root cause analysis
Root Cause Analysis (RCA) is usually a step in a larger problem solving exercise. There are multiple tools that may be used during a Root Cause Analysis. Some of them can sometimes be completed by one person, but in most cases a Cross Functional Team (CFT) approach will reap the greatest benefits and increase chances of reaching the true “root cause”.
There are also several problem solving methods that use Root Cause Analysis within their problem solving process, such as 8D Problem Solving (8D) and Six Sigma / DMAIC. The root cause analysis is a critical step in each of these examples.
It is the group of problem solving approach, to identify the root cause.
It is important to fix the problem, don’t fix the blame…..!

So lets dive into the systematic step-by-step root cause analysis methodology,
Here are below root cause analysis steps, we go step-by-step.
Define the problem
In every customer complaint or in internal failure include the high risk of rejection and cost. And we always looking to fight on these problems, in this scenario if we are not identify the correct problem then our strategy or study to eliminate those problems goes wrong. Then at the end, we spend lot of time and cost to eliminate problem is not effective and not get you the desire results.
It is the way of systematic representation of problem, if you are not define the problem properly. It will leads to wrong way, and we cannot find the right solution for the same.
– Identifying ‘What is wrong with what’
– Detailing the problem in quantifiable terms
Use 5W / 2H Questions, for defining the problem.
Who – Identify which customers complaining? / Who is affected?
What – Identify the problem adequately and accurately.
When – Timing …When did the problem start?
Where – Location …where is it occurring?
How – In what mode or situation first the problem occurs?
How many – Magnitude …quantify the problem.
Why – Any known explanations contributing to the problem should be stated.

You can read more about the 5W-2H methods.
Find out possible causes
After defining the problem, next step is to find out the possible causes for the problem generation. Therefore here we are going to find out possible causes.
There is a most powerful tool to identify those possible causes is Cause & effect / Ishikawa diagram. (Fishbone diagram)
The method consists of systematically identifying all the sources, that may contribute to the problems under investigation. It’s generally done in a brainstorming session with a team of people who are knowledgeable in the problem area.
The steps include in cause and effect analysis is,
1. Form a team
2. Find out the possible causes from each team members
3. Draw this causes in 4M categories in cause and effect diagram
4. Filter out the most probable causes from all of possible causes
5. Validate each probable cause, either cause is valid or not
6. Find out the root cause from probable cause.
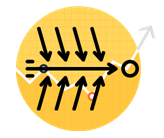

To learn more about the cause and effect tool.
Lets take an example how the causes is draw in cause and effect diagram,
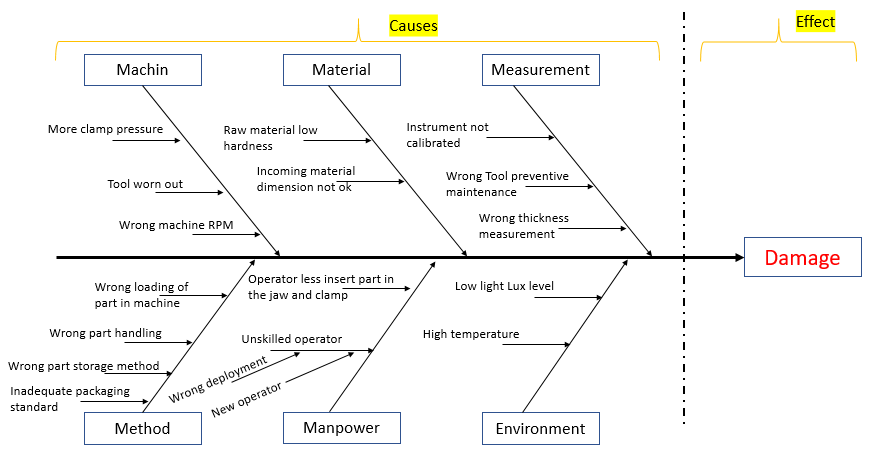
We had a problem here relating to the failure of Damage (Shown in Fig.), after investigated / brainstorm by a team in assembly shop. So, the team sat together and just talked to all the people involved in the process, looked at the process and here’s the example of their fishbone diagram. Now, maybe here we don’t need to go through everything that you can see. All of these resulting then in a damage failure. So you can see how creative this can be and it doesn’t have to be perfect but you get all the ideas into the diagram.
After creating the Cause & effect diagram, we have the possible causes to generate the damage failure. Now the team would vote to select the most probable causes from possible causes. So normally everyone votes to pick causes that need to be investigated further through experimentation and analysis technique.
Root cause identification
Now this is the key term for our tool, root cause. In the same vein we find out the probable cause and which is valid cause for the problem.
Therefore here we are going into deep to find out the root cause. To identify the root cause there is a method, called why-why analysis.
Use Five why for the potential causes to get the system root cause:
After found out the valid cause use the Why-why analysis tool to get the root cause for problem generation and escape.

Likewise use the why why question method to get the final root cause. And take action on that cause to eliminate the problem.
Implement solution
Now what can you do to prevent the problem?
Its nothing but to implement the solution for that problem. Therefore here we are going to find out the solution for the root cause.
When we implement the solution for the root cause, then the cause will not be generate in future. And that’s why the problem also not reoccurs in future.
Also one of the way you can identify the solution for the causes is Failure mode and effect analysis (FMEA).
You can do RCA study in various field, in many life cycle problems by following above steps. Such fields as Root cause analysis in testing.
Also you can find the root cause analysis software or root cause analysis templates to conduct the study.

I am a full time Engineer and Quality Professional with over 11+ years of experience in the automotive industry. My professional journey has started from a small enterprise quality inspector to a advanced quality expert. I am creating a good-quality content for engineers. Help them to grow in their career.Learn more here.