Procedure for inspection and testing is crucial for monitoring and tracking good quality products.
Inspection and testing are the methods of identify and control the defects in our processes.
When a quality engineer starts their journey in industry it starts with measurement. This is done using some inspection and testing methods. Also acceptance of good parts are done using such methods.
According to IATF 16949:2016 & ISO 9001:2015 every organization must have the procedure of inspection and testing.
Therefore for audit and Quality Management System point of view this complete article will help you to learn and understand the complete procedure of inspection and testing.
Let’s get started,
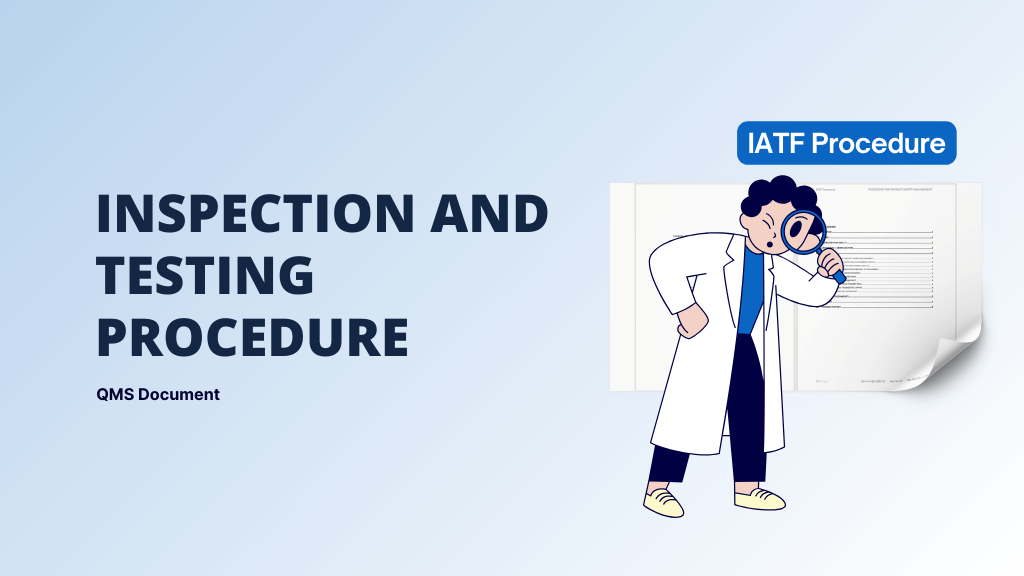
Procedure of Inspection and testing explained
1. PURPOSE
To establish and maintain a system for Inspection and Testing at all stages of processes in manufacturing operations.
2. SCOPE
Applicable to all parts, materials and products at all stages of manufacturing.
3. DEFINITION:
Nil
4. RESPONSIBILITY
- Quality Head is overall responsible for inspection and testing of incoming Raw Materials, in-process and final products.
- SQA are responsible for calibration of measuring instruments related to product and process inspection and testing.
- Quality supervisor responsible for status identification (tagging system)
- Quality Engineer responsible for maintain record of inspection and testing
- Production supervisors are responsible for in-process material checking and release for further processing. Quality inspector will cross check the material released by the production team.
5. PROCEDURE
Receiving Inspection
Receive material GRN from Stores inform arrival of material in organization. By the time material is handed over and kept in an under inspection area.
If material received along with test reports by the supplier then after reviewing all reports supplier quality perform incoming inspection and testing accordingly.
Do a sampling inspection of material based on a control plan.
Check/test the samples for the required specifications and maintain records in dimensional inspection report/Lab report.
Compare the results with the values given in respective Inspection Standards.
If material is found as per the specifications then accept the batch/lot and send reports to Stores.
If material is ok then material is transferred to the RM store with ok/acceptance tag along with a report.
Such material is then released for further processing on line.
In case the material is found rejected, mention the reason for rejection on red tag and incoming inspection report and transfer the material in red bin rejection area.
Also intimate to supplier using proper mail communication through purchase department for the non-conformance and ask for corrective action and 8D report.
FPA & In-Process Inspection
Production persons do checking and released the parts further. Do sample inspection of those released in-process parts as per sampling plan and control plan.
Prepare the line parts inspection report. Maintain records of those inspection and testing of in-process parts.
Maintain inspection reports with status of conformance/non-conformance of the product.
Accepted parts release to next user section with confirming tag on material.
Check the components at each stage of operation as per the control plan /operational standards.
Maintain records till record retention period defined as per QMS standard.
Carryout patrol inspection and testing at each stage of process operation as per control plan.
Maintain such record of in-process inspection.
In case the material is not meeting the specified requirements,inform the same to production supervisor, try to stop the production and record the same in inspection report with time.
Final Inspection & PDI
Final inspection shall be carried out as per control plan.
This inspection covers Visual and Dimensional inspection and other testing specified in control plan to validate final product.
Segregate the non-conforming material in red bins and conforming material to other normal bins.
Record the inspection and testing result report as final inspection report.
Tag “OK” green tag with signature as approved material and release for dispatch to customer.
Provide “Reject” red tag on non-confirming material indicating reasons of rejection and quantity with signatures. Those material found rejected and handle the non-conforming product as per control of non-conforming products procedure.
Provide “HOLD” yellow tag with the status of material requiring a pending decision for acceptance.
After final inspection but prior to shipment carry out PDI (Pre-dispatch inspection) or dock audit` to verify conformance of product, packaging and labeling as per specified requirements.
Layout Inspection & Functioning Testing
As per layout inspection plan (Once in a year or as required), all printed dimension mentioned in drawing shall be verified and inspected. Keep record of layout inspection and maintained to retention period of time.
The results may be sent for customer approval if there are any customer specific requirement.
6. REFERENCE DOCUMENTS
- IATF 16949:2016 Standard
- ISO 9001:2015
- Change Management Procedure
- Training Procedure
7. RECORDS
F-QA-02 | MASTER LIST OF CONTROL PLAN. | 01-02-2018 | |
F-QA-03 | LIST OF LIMIT SAMPLES | 01-02-2018 | |
F-QA-04 | MASTER LIST OF QUALITY ALERT | 01-02-2018 | |
F-QA-05 | QUALITY ALERT | 01-02-2018 | |
F-QA-06 | INCOMING INSPECTION STANDARD | 01-02-2018 | |
F-QA-07 | MASTER LIST FINAL INSPECTION STANDARD | 01-02-2018 | |
F-QA-19 | RAW MATERIAL TESTING PLAN | 01-02-2018 | |
F-QA-20 | INCOMING INSPECTION REPORT | 01-02-2018 | |
F-QA-21 | FIRST AND LAST PC APPROVAL REPORT | 01-02-2018 | |
F-QA-22 | LINE INSPECTION REPORT | 01-02-2018 | |
F-QA-23 | FINAL INSPECTION REPORT | 01-02-2018 | |
F-QA-24 | DEVIATION RECORDS | 01-02-2018 | |
F-QA-25 | CUSTOMER RETURNED RECORDS | 01-02-2018 | |
F-QA-26 | INCOMING PPM DATA | 01-02-2018 | |
F-QA-27 | INPROCESS PPM DATA | 01-02-2018 | |
F-QA-28 | CUSTOMER PPM DATA | 01-02-2018 |
Download inspection and testing procedure template

I am a full time Engineer and Quality Professional with over 11+ years of experience in the automotive industry. My professional journey has started from a small enterprise quality inspector to a advanced quality expert. I am creating a good-quality content for engineers. Help them to grow in their career.Learn more here.