In manufacturing industry as a Quality Engineer you are aware of process. We think inspection is the good process to avoid defect passing to customer end. But we must know Why inspection is failed to prevent defect.
Regular concept
Preventing defects; there’s a lot of costs going into preventing but, you’ve got to make sure that you have the right type of prevention.
So we were just saying automatic checks, you’ve got to put the time in and if you just have an inspection at the end of the process, you’ve got these non-value-added costs and capital, just for the inspection.
And of course, you’ll still end up with scrap or rework cost, rather than having prevented the defects. All the way at the beginning and inspection is never perfect, as we were talking about the external failure cost.
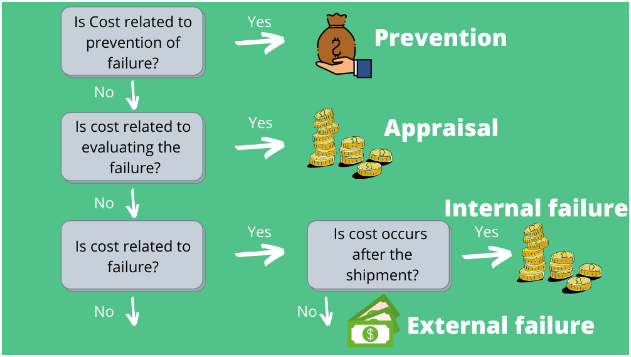
You can end up some of those defects may slip through, and pass to the customer. And that can be then lead to very large problems, if when the defects get out into the field.
Additionally, again with the idea of culture, inspecting at the end removes responsibility. And again, not that we want to finger point. But as soon as you find where the defect occurs, you can look at it and attack it right away, rather than waiting until the end. And you can end up, quite off of fighting that you have a bottleneck in your process just at the end, at the inspection point.
So, prevention typically cost less, than the combination of all the inspection, internal and external failure costs. And how do you do this? you want to develop capable business processes, through standardization and continuous improvement, for which you need to achieve using six sigma process.
Conclusion
Inspection at the end is only creating bottleneck in the process.
Also prevention of defect is effective than to detect the defect through inspection process.

I am a full time Engineer and Quality Professional with over 11+ years of experience in the automotive industry. My professional journey has started from a small enterprise quality inspector to a advanced quality expert. I am creating a good-quality content for engineers. Help them to grow in their career.Learn more here.