Quality is define differently and even name and termed differently. And we continuously learn these terms. We must need to know the basics and TQM fundamentals.
Now here in this post we will look into the key fundamentals required in Total Quality Management (TQM).
The concept and understanding of the TQM involving terms in details,
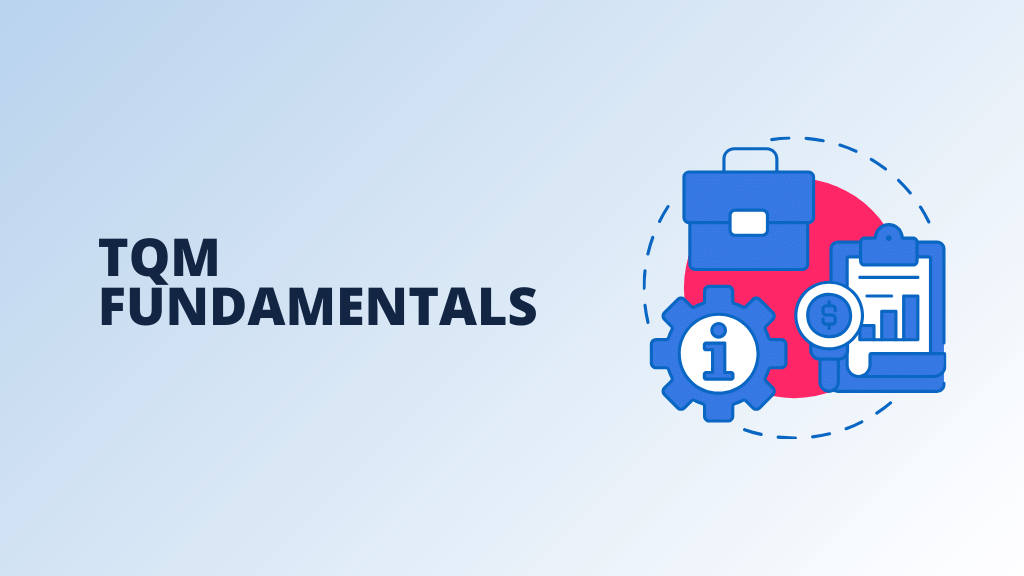
What do you mean by Quality?
Dr. Juran stated that, Quality means fitness for use. Therefore it includes reliability, availability and maintainability.
However a more precise definition, we could say is fitness for use and meeting or exceeding customer expectations.
And in the ISO 9000 : Quality is the degree to which a set of inherent characteristics fulfills requirements.
Also, another definition of quality which is worth quoting is from Dr. A Blanton Godfrey. A modern day quality guru, and in a 2002 article he says,
The most fundamental truth is that, Quality is relative; the customer focus is simply on value, seeing it as a ratio of quality over price and only when we offer more value than our competitor, do we really succeed.
Professor Godfrey, A. Blanton (2002), “What is Quality?” Quality Digest, January, pp. 12.
And this definition, goes beyond the idea that,
Quality is simply being fit for customers’ use.
Quality includes customer satisfaction.
And it includes efficiency in production and price competitiveness.
Also it conveys the idea that, not only is it enough for customers to make the products with the right characteristics. But, the business needs to make a profit.
You can learn more about how to define quality?
Why Quality Management?
For understanding this concept we will go through the old and new belief systems. So that this will be better way to understand.
OLD BELIEF : Quality comes from inspection
In this belief, the product is go through the process. At final it would be inspected.
Then we can decide the quality, either it is good or scrapped or possibly reworked.

Preconception was that, quality means to test, it means additional resources used for testing, time used for testing.
This is very costly, this reduces your throughput, cost manpower and it’s very very reactive.
NEW BELIEF : Quality comes from Management
In the new belief, management plays important role to perform quality products.
It is the management approach to long term success through customer satisfaction.
All the members of an organization is participating to improve processes, services, product and culture in which they work.
“Quality means doing it right when no one is looking..”
Henry Ford
To achieve this new approach we need to follow the Total Quality Management (TQM) methodology.
Quality Improvement
It is the essential activity in TQM.
When we are failing to achieve the quality through current methodology. Then we need to make the improvement plan.
The aim of the improvement is measuring where you are. And find out the way to make things better.
It is specially actions to avoid blame and to create a system to prevent the errors from happening.
Inspecting and finding the bad one and throwing them out is too late, ineffective and costly too. Therefore the quality is not comes from inspection but it can achieve from improving the process.
Various tools & approaches used for improvement.
5S, Kaizen, QC tools, Lean, Design of Experiments…
It includes the involvement of all people in quality improvement.
To achieve the improvement training, communication and recognition is necessary.
Total Quality Management
There are many aspect of quality,
It is the big-Q,
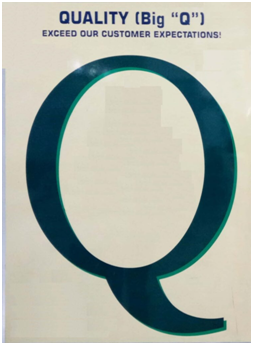
- Quality in Manufacturing: Less number of defects, Efficient Process (Less cost)
- Quality in design: Less number of failure & product meet market quality & cost expectation, timely completion.
- Quality in maintenance: Maximum uptime of the machine, No quality / productivity problem due to machine
- Quality in HRM: Skilled manpower, participation of all in improvements, Employee satisfaction, employee engagement & safety
- Quality in purchasing: On time & good quality product supply for manufacturing, Less rejection / rework at supplier end
Quality management is not achieving product quality, it is achieving Quality-Cost-Delivery-Safety-Moral.
Summary of TQM fundamental
Quality control as well as quality assurance both needed in TQM fundamentals.
Employee engagement and employee are most important asset in total quality management.
Quality improvement is the key for drive the business.
Decision should be base on fact rather than opinion.
Every process is having the variation, and it can be in control.
Quality is nothing but meeting all stakeholder expectation.

I am a full time Engineer and Quality Professional with over 11+ years of experience in the automotive industry. My professional journey has started from a small enterprise quality inspector to a advanced quality expert. I am creating a good-quality content for engineers. Help them to grow in their career.Learn more here.