Supplier management is the core concept during the development stage. The role of supplier management is leading to achieving a zero-defect culture during the initial development stage.
Why the supplier management is important in the engineering and development process?
As you see in the industry, you have many options to buy products. And each place there is a difference in the quality of that products. The quality is being judged by your requirement in terms of durability, aesthetics, and reliability, etc., etc.
Now you need to choose the best supplier among these all. So, what are the factors on the basis you select them? That can be the size, dimensions, appearance, feel, ratings, etc., etc.

And here is the main purpose of supplier management to plays role. It is the structured process of identifying the best supplier with the help of a team. If you identify the best supplier automatically your customer satisfaction will improve.
In this way, supplier management is very important to choose the correct supplier.
What are the factors of good supplier management?
- Strong team approach
- Risk Assessment
- Follow APQP process
- First time right PPAP

1. Which teams are involved in supplier management?
The point where risk assessment comes into role. The Purchasing, Engineering, Quality, sales, and Program manager are involved to anticipate the risk associated with suppliers during the initial development process.
To check technical feasibility, Engineering and purchasing play an important role. Where they check supplier can meet the technical requirement or not.
The Program team is taking care of the document’s formalities. Such as signing contracts and legal documents.
Now the Engineering team will investigate design reviews and validation activities.
The tool experts play role in the industrialization and tooling process. Further SCM and SQA personnel take care of packaging and validation of product to quality.
At the last, the PPAP concept is there where the engineering and SQA team will be taking care of PPAP activity.
2. What is risk assessment in supplier development?
Now, the first step is to identify the risk related to the supplier at the initial partnership. The risk must be assessed before the finalization of the supplier based on the defined criteria.
The criteria for risk assessment can be,

- Quality Performance of supplier
- Financial condition
- Machine/resource availability
- Technical expertise in the field
- Location availability
- ……And many more
In this assessment, you know the area of risk associated with the supplier. This risk can be reduced based on an action plan and follow-ups.
Once the risk is assessed then the supplier is selected, and further process will be evaluated.
In the next step, there will again be more parameters needed to check such as commercial performance, logistics, capacity, quality commitment, etc., etc.
It will check the feasibility of the product by the supplier process is evaluated. And making the supplier in the approved supplier list and the contract/agreement has been signed with the supplier.
3. How does APQP help in supplier management in the development phase?
We have seen that suppliers have been selected / onboard once all risk is considered. Then the supplier will be taking part in the development process. It means the supplier components are also part of our development plan.
Now all APQP process is followed by the supplier. To fulfill the requirement supplier should follow the Supplier Manual.
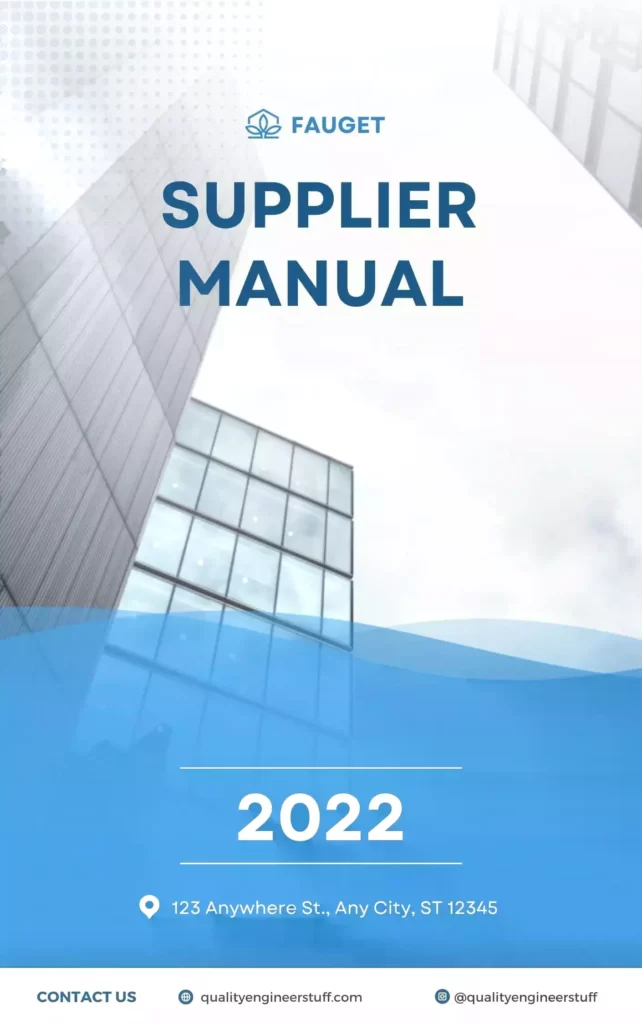
Learn the complete APQP Advance Product Quality Planning) process in an easy way.
- If the product is of supplier design, then we need to align the Special Characteristics (SC or CC Characteristics) with the supplier. And check the DFMEA reports of the supplier to verify that all the severity points are considered or not.
- Now you need to enter into the supplier process. Where you need to check every element in the process for a safe product launch. Here all documents is been checked such as the Process flow chart, PFMEA, and control plan to ensure production process validation for good supplier management. Checking the validation of all tooling s and equipment.
- Then check the expected quality level and packaging of the supplier. Where the Run at Rate has also been evaluated.
- Based on all the above activities the supplier is to submit the PPAP as per requirement.
4. Final step of the supplier management in the development stage.
Here you have the interim PPAP of the supplier. So the parts must be qualified using Supplier Quality and certified as OK parts based on specification/plan.
Now at end of the supplier management process, you need to check whether all requirements are fulfilled by the supplier or not. It includes many points such as
- PPAP validation should be complete and approved.
- Appearance approval must be done.
- All ECRs should be close or managed by all validation rules to avoid any further risk.
- Supplier process capability to be validated.
Conclusion
Finally, you can say now that you have followed the supplier management process during the development stage to assess all risks associated with supplier selection.
Then you approved the supplier based on the requirement and criteria. The supplier is now onboard with your programs.
Now, you follow the APQP process to align the supplier product with your APQP plan. Once all the activity has been validated the supplier is ready to provide the parts as per your requirements.

I am a full time Engineer and Quality Professional with over 11+ years of experience in the automotive industry. My professional journey has started from a small enterprise quality inspector to a advanced quality expert. I am creating a good-quality content for engineers. Help them to grow in their career.Learn more here.