Learning and implementing FMEA-MSR is difficult due to lack of good content, explanation and understanding.
Standards, presentations and other training material have lot of technical statements which are not easy to understand. Therefore we are skill in our career. end up learning the topic and lack with FMEA-MSR This article will provide you the detail guidance on FMEA-MSR topic with very simple way.
The below process gives me better clarity and master in the concept of FMEA-MSR topic.
FMEA MSR full form/meaning:
The full form of FMEA MSR is Failure Mode and Effect Analysis for Monitoring and System Response.
What is FMEA-MSR?
The FMEA MSR study conduct to analyze the potential failures might happen in the customer/vehicle operating condition.
This is something when your product or system is use in the vehicle and if there is a failure, then we can analyze, what are the failure and their impact on the Vehicle, System, Driver or people.
Whether the driver can detect the failure effect or the system can detect the failure mode or failure cause are the point of analysis in FMEA-MSR.
The scope of operating conditions includes the End-user operation or in-service operation or maintenance operation.
Now, you may have question that we can also do the failure analysis in the Design FMEA to analyze their effect on system, customer and End-user level, then Why FMEA-MSR?
Why FMEA-MSR? Purpose of FMEA-MSR
When there is an Electrical/Electronic system, the risk is the malfunction of the E/E system. This Malfunction due to the fault in the system, and it will have an effect on vehicle operating function.
The E/E system considered as mechatronics system. Which consist of Sensor Actuator ECU (Electronic Control Unit).

Now, there is a need of monitoring and response by the system. If any Malfunction happen, then it is detected by the system or user and the risk is at acceptable residual risk.
Therefore the FMEA-MSR helps to reduce the risk by monitoring response and fault detection using some diagnostic monitoring and system response.
Sometimes it helps to identify additional mechanism for diagnostic and monitoring purpose. The concept of fault detection and diagnostic monitoring helps to achieve vehicle safety goals and safe state of operational situation.
The FMEA-MSR evaluate to detection of fault/failure cause in the customer In general th operating condition. Then response to eliminate the more severe effect and replace with the less severe effect, that is acceptable risk.
How to create FMEA-MSR?
The methodology of FMEA-MSR is according to AIAG-VDA FMEA 1st edition 2019. And it has the similar steps as we learn in DFMEA and PFMEA.
But the content in those steps are different than our DFMEA and PFMEA method.
Therefore the 7 step approach use for creation of FMEA-MSR are as below.
- Planning and Preparation
- Structure Analysis
- Function Analysis
- Failure Analysis
- Risk Analysis
- Optimization
- Result Documentation
Let’s learn each step in details,
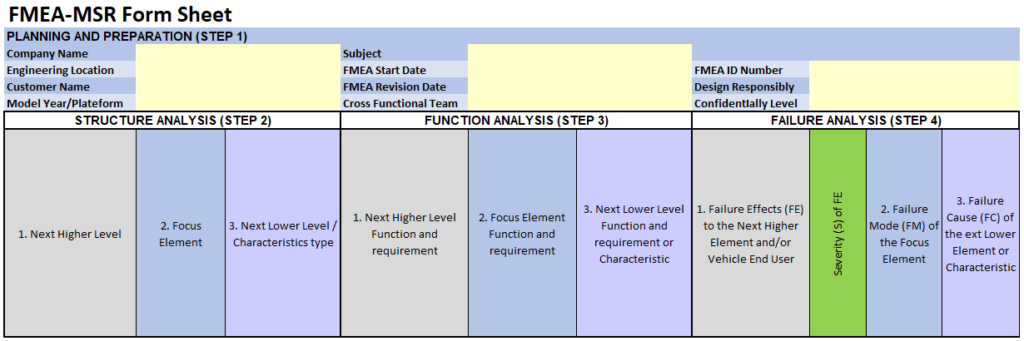
Step 1: FMEA-MSR Planning and Preparation
Planning is crucial for the project success. Therefore in the planning stage we need to understand the product concept / inputs required and project plan to do the FMEA-MSR.
Product concept:
What is the system or product we will create the FMEA for?
Product understanding:
Here we need to look the inputs require for analysis, for example,
- Hazard Analysis and Risk Assessment
- Legal and Regulatory requirements
- Product Functional / technical requirement
- Customer specific requirement
- Product structure (Block/boundary diagram)
- Drawings (2D, 3D)
- Bill of Material
- Reference FMEA’s
Above inputs needed to understand the project and effective FMEA creation process.
Project scope: Project Identification and Boundaries
In every analysis it is important to define the scope first. In the project scope define what is include and exclude from our study.
The block diagram will be the correct inputs for us to understand the scope and system overview for the analysis.

Project Plan – 5T method
5T method is the 5 steps to do the project planning. Those 5T’s are as below.
- Team
- In Tent
- Time
- Task
- Tool
It is the big topics and you can learn complete concept of 5T project planning article.
FMEA-MSR template Header.
The header information is also the part of planning and preparation step. Where we fill the details about system information.
Step 2: FMEA-MSR Structure Analysis
Once the scope is define using the inputs. The structure tree created for the system.
The structure analysis will visualize the analysis scope. Shows interfaces and interaction for further analysis.
The important inputs require to do the structure analysis is Block Boundary Diagram and Bill of Material.
Block boundary diagram provide us the information of system and their interfaces.
Bill of Material will provide us the hierarchy of the system, assembly and components with their levels
You can refer the Structure Analysis below for example.
@Structure Tree @
Here structure analysis is completed, lets jump to step 3.
Step 3: FMEA-MSR Function Analysis
The functions of the system is, What is the system intended to do?
For monitoring and detection mechanism of the system fault/failure are considered as the functions.
We say the E/E system consist of Sensor, Actuator and Control Unit. Now what actual work of sensor, actuator and control unit in the system are considered as function.
Function analysis step is very much similar to the DFMEA function analysis.
@Function Tree @
Step 4: FMEA-MSR Failure Analysis
Failure Analysis is always a heart of FMEA study. Failure analysis gives you the idea that how your system can fail.
In FMEA-MSR the functions of operating conditions already identified. Now it’s time to find out how the function might fail. Those will be your failures.
As we talk about the FMEA-MSR then it means the system will interact to vehicle operating condition and consist of E/E system.
Then we first understand the overview of impact/effects of E/E system Fault to user, vehicle or system level.
When fault happen it will leads to malfunction behavior of system. Malfunction will disturb vehicle/system operating condition and the failure effect happen.
There are three failure effect considerations,
- Non-Hazardous
- Hazardous
- Mitigated
Non-Hazardous Failure Impact/Effect

In this consideration fault leads to malfunction behavior and malfunction will create impact of Failure Effect and there is no hazardous event.
Hazardous Failure Impact/Effect

In this example the fault leads to malfunction behavior and malfunction will create impact of Failure Effect and there is hazardous event.
Mitigated Failure Impact/Effect

In this example the fault leads to malfunction behavior. Then system will detect and monitor response and will have a less severe effect than original failure effect. It mean mitigated failure effect but no hazardous event but loss or degradation of function.
Hope you have understood the failure effect examples,
Now we jump to the topics failure cause, Failure Mode and Failure Effect.
Failure Cause:
In FMEA-MSR the failure cause is nothing but the fault of E/E system. This is something the fault happen at system level during vehicle operating condition.
Its not consider as root cause. Because the root cause is at hardware or component level and leads to fault.
The Failure cause is the Fault in the system.
Failure Mode
The failure mode is nothing but the malfunction behavior of the system due to fault.
For above example of failure effect, hazardous and non-hazardous event the failure mode is same as the failures mode observed in DFMEA.
But mitigated failure effect case, the failure mode is different. Which diagnostic monitoring response failure.
Failure Effect
Failure effect is what we zee o above examples.
Those are the impact on the vehicle, user or system due to failure mode (Malfunction Behavior).
Step 5: Risk Analysis
The risk analysis step covers the evaluation of risk based on the failure severity (s), Frequency (F) and Monitoring (M) ratings.
The rating given based on the failures occurrence, impact in vehicle operation and their monitoring controls.
Overall risk analysis will consider the points below.

- Severity (S) rating of failure effect
- Rational for frequency rating
- Frequency (F) rating
- Current monitoring control
- Monitoring (M) rating based on monitoring control
- Action Priority Risk Evaluation
Severity (S) in FMEA-MSR
Severity rating in FMEA-MSR given based on how severe the failure effect of our failure mode.
The severity rating given in the scale of 1 to 10 according to FMEA-MSR severity table below.

Rational for frequency rating
In FMEA for monitoring and system response the failure will occur in the field or customer/vehicle operating condition. Therefore we need to assume that our product is made well and focus on how the customer uses it. This way, we can see if our design is good enough.
In the rational for frequency table we need to mention those assumption of consideration for the Frequency rating.
Examples are
- Standards
- Data Handbook
- Customer complaints
- Warranty data
- DFMEA and PFMEA results
- Etc.
Frequency (F)
The frequency rating is based on how frequently the failure cause happen in the field or in customer operating condition.
Sometimes the failure effect can be due to multiple cause and we may not have the occurrence data then we should use data of the probability of exposure to certain.
Operating situation.
The Frequency rating given in the scale of 1 to 10 according to FMEA-MSR frequency table below.

Current Monitoring Control
The actions or controls are already implemented to detect the failure cause or failure mode or failure effect should be add in the current monitoring control column.
The Failure cause (fault) and failure mode (Malfunction behavior) control by the system monitoring and Failure effect (harm or hazard) can be detected by the system or driver.
Monitoring (M)
Monitoring rating is depend on how strong detection you have against the fault of E/E system. The monitoring mechanism includes all components and system such as sensors, actuators, diagnostic mechanism.
Fault/failure will be detected and as a response it will modify the system behavior so that the effect will be mitigated to safe state.
FMEA-MSR Monitoring Table
Refer the Monitoring (M) rating table below,

FMEA-MSR Risk Evaluation
Once you identify severity (S), Frequency (F) and Monitoring (M) rating, it is time to evaluate and prioritize the actual risk.
And the risk is prioritize base on action priority. Once the risk is identify then management should review the risk and appropriate action is needed to reduce or mitigate the risk.
Action Priority (AP)
In Action Priority the risk determined based on (S), (F) and (M). The risk is categorized in three levels.
- Low (L)
- Medium (M)
- High (H)
Low (L) action Priority: Team could do the review of Low (L) risk. And if want then can add the better monitoring control to improve the system.
Medium (M) action priority: Team should do the review and identify the appropriate actions to reduce the frequency (F) or improve the monitoring (M). If no action or controls identified further then justify your comment and document why current controls are enough.
High (H) action priority: Team should do the review and must identify the appropriate actions to reduce the frequency (F) or improve the monitoring (M). If no action or controls identified further then justify your comment and document why current controls are enough and communicate the risk to the management, customer and interested parties.
You need to add the actions for all High (H) and Medium (M) AP risks to improve the safety of E/E systems.
FMEA MSR Action Priority (AP) Table
Refer Action Priority (AP) Table below,

Step 6: Risk Optimization
The risk is identified and categorized in the step 5 risk analysis. Now the purpose of the step 6 is to reduce or eliminate the risk using some appropriate actions.
The risk is reduce/eliminate by either change in components design to reduce the frequency (F) of failure cause or improve or design the monitoring system for better detection capability.
The new actions must be fulfill with all requirements below.
- Responsible person names
- Status of action
- Target completion date
- Check effectiveness of action taken
- Refer optimization table for reference below,

Step 7: Result Documentation
Once the step 6 risk optimization completed, its time to communicate the results to the management and interested parties.
That’s why the step 7 result documentation is needed.
The FMEA-MSR report along with the action plan should be communicate to the team and management. Sometimes the auditor also check the output of the study.
The result documentation clearly mentioned all relevant documents such as,
- Scope definition
- Project planning (Pan vs Actual) 5T method
- FMEA-MSR filled template
Conclusion
That’s everything about the FMEA-MSR. We have tried to make this article in detailed and yet in simple language. Kindly go through each point in detail for better clarity about FMEA- MSR topic.
You can have a look to FMEA sitemap in sidebar at top for all topics related to FMEA Also join the community to get such detailed and important articles early.