The terms CORRECTIVE ACTION and PREVENTIVE ACTION have always been used for improvement purposes. So, here we look into the detailed corrective action procedure.
Corrective action is always taken into account when a problem occurs.
The problem can be a form of a Customer complaint, Internal rejection, defects, Audit non-conformity or process issue, etc.
Let’s have a look into the procedure,
Corrective Action Process Flow
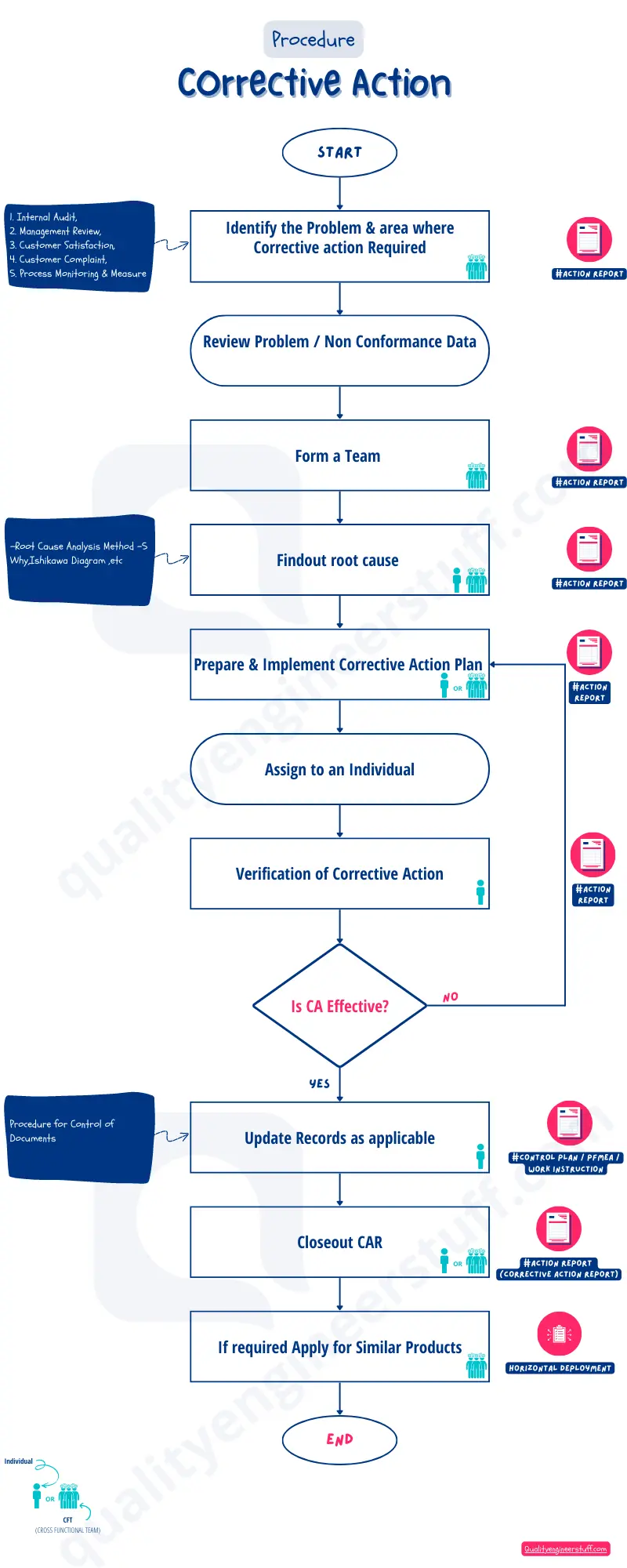
Corrective action procedure Explain
Let’s discuss all processes in detail,
1. Identify the Problem & area where Corrective Action Required
Problem identification is the first step to starting corrective action implementation.
The problem identification can be made using many media. Such as from customer complaints you will get the problem or issue faced by customers.
You will get the non-conformity in Audits. To close this non-conformity you need to initiate the correction action plan.
2. Form a Team
Once you identify the problem, to resolve you need to form a team. The team includes all responsible functions. We can call it a Cross-functional Team or Multi-Disciplinary Team.
3. Find out the root cause
The CFT team is responsible for identifying the potential causes of the problem occurrence.
You can use the Cause-and-effect diagram to identify the potential causes using the brainstorming method.

From all these causes you need to identify the possible causes and using root cause analysis you will find the exact Root Cause of the problem.
4. Prepare & Implement Corrective Action Plan
After getting the root cause next step is to find a solution.
Corrective action should be taken to eliminate the root cause of the problem. The corrective action will be planned and implemented to avoid the re-happening of the problem.
5. Assign to an Individual
Assign the corrective action plan to the individual / respective team to complete within the timeline.
6. Verification of Corrective Action
After the implementation of the corrective action, we need to verify the action. It means is it effectively implemented and what is the result after corrective action is taken.
7. Is CA Effective?
There is a decision after verification of corrective action. The decision either the corrective action is effective OR the corrective action is not effective.
The next step depends on this decision.
Is CA Effective: No, Then you need to go back to step 4 to find out another corrective action.
Is CA Effective: Yes, Then will initiate the next step
8. Update Records as applicable
If the corrective action is effective and the problem is resolved, then update the records.
Update records mean it needs to update these action-related points in the standards.
The records can be a control plan, FMEA, work instruction and forms or format or daily monitoring reports, etc.
These steps will ensure that we standardize our system to take care of the problem in the future.
9. Closeout CAR
In this step close the Corrective Action Report, as we have successfully identified the root cause, and taken corrective action and it is effective enough to resolve the problem.
After sign-off reports will send to the customer. Customer communication on resolution of the problem.
10. If required Apply for Similar Products
It is important to implement the same action for similar product or process. Because the same problem can happen for other similar product.
It is the proactive approach that we do the horizontal deployment of actions.
Corrective action procedure pdf
Conclusion
Problem identification done through customer complaint, audit non-conformity, management review, process monitoring and measure, etc. Then Form the team, next is to find out the root cause. Take the appropriate corrective action. Effectiveness must be check so that our corrective action is effective or not. Update all standards and records for sustenance of action. Submit reports to customer if applicable. Then implement the same action to the similar product as proactive approach to avoid the failure in other products.
Please write us on “support@qualityengineerstuff.com” for any special topic post as per your requirement.

I am a full time Engineer and Quality Professional with over 11+ years of experience in the automotive industry. My professional journey has started from a small enterprise quality inspector to a advanced quality expert. I am creating a good-quality content for engineers. Help them to grow in their career.Learn more here.