The 8D (Eight Disciplines) methodology is a systematic problem-solving approach designed to identify, correct, and eliminate recurring issues, particularly in product and process quality. Developed by Ford Motor Company in the late 1980s, it has since been widely adopted across various industries for its effectiveness in addressing complex problems.
Disciplined Problem Solving is essential
Hello everyone in this post we learn & explain 8D analysis problem-solving methodology.
Introduction of 8-D Methodology
Today we want to explain the
- Purpose of the eight disciplines for team oriented problem-solving
- Understand the importance and the interactions of each of the disciplines
- Use the 8D methodology for problem solving, and for corrective and preventive action implementation.
We established cause-and-effect relationships, therefore we built hypotheses for improvement and used statistical analyses to verify these improvement ideas. And then finally we established long-term sustainability through process control.
Now, as we said, business success means reducing the variation and centering our critical to quality parameters leading to reduced costs, reduced defects, improved productivity, reduced cycle time, better matching our customer needs, so that which may lead to an increased organisational profit.
In this post, we want to introduce the 8D, which is a problem-solving methodology. So 8D focused on identifying, correcting and preventing a problem. The 8Ds have their origins in the United States military and in the automotive industry. Ford documented the 8D method in the late 1980s. And the method defines eight disciplines or stages, and there’s a new stage added, state zero.
8D is used for handling customer complaints and re-occurring process problems. Once it happens you grab a team, then you need to understand the problem and take containment actions. You need to find the root cause and choose a corrective action, implement the corrective action and then learn a defined prevention for the future before you release and congratulate the team.
what is a problem?
Now, we looked earlier at control charts which proposed by Dr. Shewart, and he talked about two different sources of variability in a process, either common causes or special causes. This type of variation is explain in the post of Statistical Process control.
Common causes is accepted as part of a process. Whereas special cause variability on the other hand produces disturbances in the process and usually increases the variability beyond acceptable levels. And special cause should be then discover and eliminated.
It is important to fix the problem, don't fix the blame....!
So as we just said, common cause variability, we would work on improving that with the Six Sigma methodology, going through the DMAIC cycle. But for something that is out of control, a problem, we can use the 8 D problem-solving methodology which we then apply to bring long term stability to our process.
Anything outside of the specifications is a defect. Now, often if we see a special cause, we could have a defect.
So how does this relate to 8D?
Well again, you know with some sort of overlap possibly, the 8D analysis helps bring stability to our process. Okay, then let’s go through the different steps of the 8D problem-solving methodology.
What is 8D?
- 8D is a disciplined process which addresses problem solving in a methodical and analytical way
- Each step of the 8D analysis Process is preceded by letter ‘D’ which stands for discipline.
- The 8D process seeks to define and understand a problem, so that by taking this approach we can continuously improve quality by eliminating the causes of problems and prevent their re-occurrence.
- Each discipline has an input and output
- the output of one step becomes input for next step.

D0- Prepare for problem solving process OR Awareness of problem
Evaluate the need for problem solving process when a symptom / problem is noted
- Does the severity, urgency, size and / or complexity of the symptom exceed the ability of one person to resolve?
Determine if there is a need for an Emergency Response Action to protect an internal or external customer
- Emergency Response Action entails reworking and replacing nonconforming or suspect material(s). In other words, sometimes this may include sorting or reworking on-site.
- The whole idea of an Emergency Response Action is to protect the customer.
- Emergency Response Action is different than an Interim Containment Action (D3)
If I had six hours to cut down a tree,
Abraham Linken
I would spend four hours sharpening the axe”.

D1- Establish the Team
The first D1 in 8D methodology is team formation.
Select a Champion
- The Champion is a designated member of management who has the authority to sanction the improvements
Select a Team Leader
- The team leader is a spoke person for the team. He ensures that progress is being made, schedules meetings and coordinates the efforts of all the team members
Select Team Members
- CFT can be created at any level of the organization. However, they should be formed as close to the process or problem and its solution as possible
- CFT typically consists of four to seven (4 to 7) members.
- Appropriate specialists can be team members or may be invited to meetings as needed.
- Most of the members are usually those affected by the problems the team is formed to solve.
Generic rules
- Team should establish ground rules
- Finalize the Decision-making criteria / Model How the decision is made
Now, then you want to form a team. Team leader should be someone who has the right expertise to solve the problem, generally the owner of the process or the area where the process occurred. And so, this person is responsible for meeting any requirements and expectations of the organization or from external customers, for example, like how fast the problem should be solved. But here, this is more the expert, the area leader.
8D moderator – not an expert.
And then finally the most important is the team members, these are people that really are the experts assigned to work on the problem with their specific knowledge, and they then need to work. So we’ll have experts, specific knowledge, They need to have the time allocated and the resource allocated so that they can work on the problem, and they need to work within the constructs of the 8D, so that this can be resolved in the proper manner.
D2- Describe the Problem
The purpose of D2 is to describe the internal / external problem by
- Identifying ‘What is wrong with what’
- Detailing the problem in quantifiable terms
- Who – Identify which customers complaining? / Who is affected?
- What – Identify the problem adequately and accurately.
- When – Timing …When did the problem start?
- Where – Location …where is it occurring?
- How – In what mode or situation first the problem occurs?
- How many – Magnitude …quantify the problem.
- Why – Any known explanations contributing to the problem should be stated.
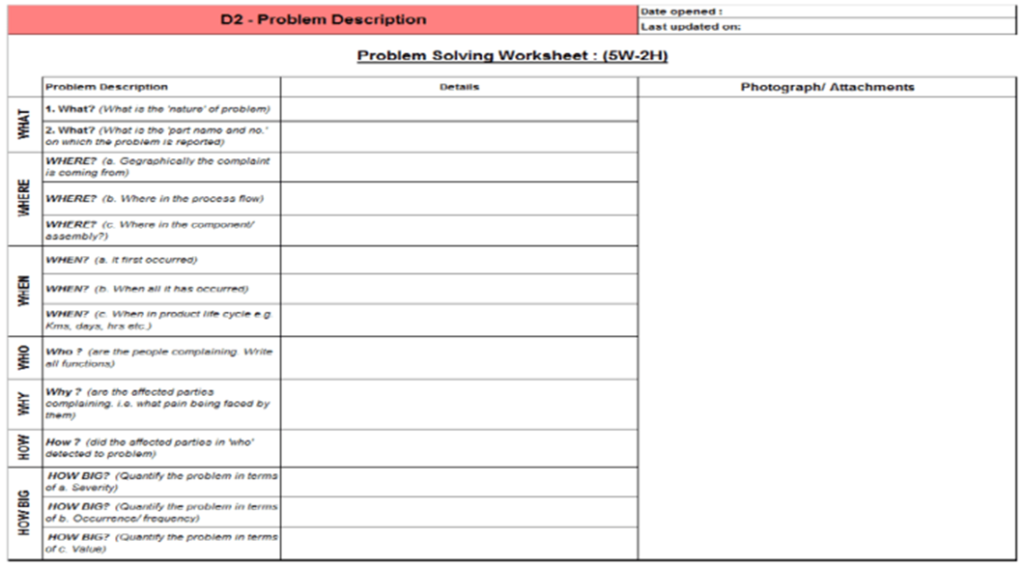
Above all the questions of 5W-2H, Read more about the 5W 2H by click here.
Conduct “Is / Is Not” Analysis (to bring in more clarity about the problem)

D1- Establish the Team D2- Describe the Problem

D3- Develop the Interim Containment Action
Define and implement interim (containment) actions to isolate the effect of the problem from any internal / external customer until corrective action is implemented
Verify the effectiveness of the containment action, so the quantifiable verification can be provided by
- SPC Charts
- Check sheets
- Dot Plots and Histograms
- Control Charts
- Paynter Charts
Protect the customer
Containment actions are used to buy time. So the principal objective is to protect the customer from experiencing additional problems.

In the Interim containment action, we have identified
1. Whether suspect material is segregate?, quarantine and tagged in the entire supply chain? (Field, warehouse, FG, in process, receipt stores and in transit?
2. Whether details are capture? w.r.t. quantity, cut off numbers, implementation dates
3. Whether specific immediate actions are clearly determine? which may include additional inspection / checks, additional operations etc.
4. Whether details are capture? w.r.t. ion qty., cut off nos., implementation dates etc.
5. Whether documented & clear work instructions are provided for the above containment and immediate actions so that there is no ambiguity while implementation & execution?
6. Whether above is communicate through document? or mail to all concerned and affected parties?
7. Whether adequate supporting data is available? & included in 8D analysis report w.r.t. effectiveness & implementation of interim actions (both containment & immediate)?
8. Whether % effectiveness of each action clearly identified based on fact and team consensus?
D4- Define & Verify Root Cause and Escape Point
Generate Potential Root Causes
Brainstorm using Cause and Effect Diagrams:
Find out the potential / possible causes using the cause and effect diagram, In addition filter out the all possible causes to very few probable causes. Then next use the cause analysis to find out valid cause for the problem generation and escape cause.
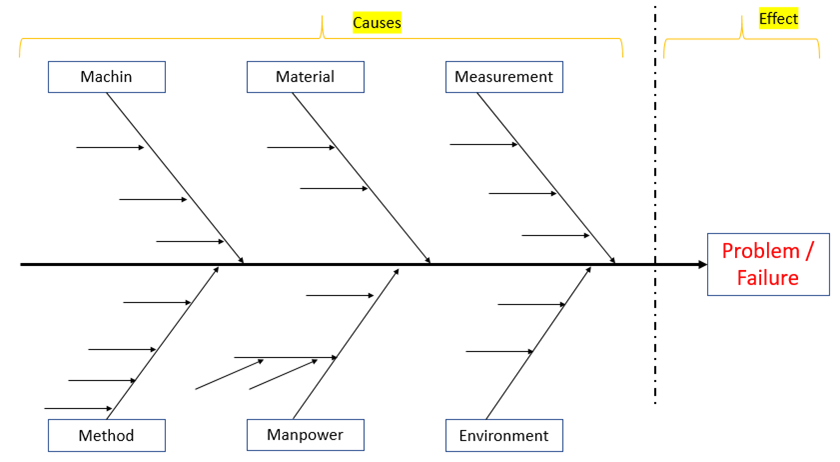
Use Five why for the potential causes to get the system root cause:
After found out the valid cause use the Why-why analysis tool, so that we get the root cause for problem generation and escape.
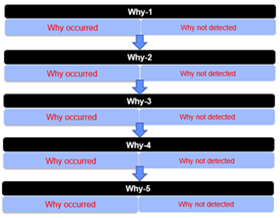
D5- Choose and verify Permanent Corrective Actions
Implement the corrective action to ensure the root causes have been removed. In other words, verify the permanent corrective action are implemented as intended.
For implementation of corrective action plan out the implementation and setup some matrix to verify long term effectiveness.
D6- Implement and Validate PCA
- Define & implement the appropriate corrective actions
- Choose on-going controls (e.g. Process sheet ) to ensure the root cause is eliminated
D7- Prevent Recurrence
However behind all root causes there are systematic issues. Therefore which need fixed to avoid the recurrence of this cause to avoid the same problem in future. So that goal of prevent recurrence is to change the system that allowed the problem to occur in the first phase
Preventing recurrence
- Notify all personnel of the resolution areas
- Update all relevant documents – Process Flow Diagrams, FMEA, Control Plan, check sheets, etc.
- Update change control records
Look for new opportunities
- Examine – similar processes
- Other locations
- Other parts in part family
Log lessons learnt from this 8D analysis study.
D8- Recognize team & Individual contributor
In this category, we have to ensure
1. Whether lesson learnt is document? and discussed with team?,
2. whether opportunity for horizontal deployment is identify?
3. Whether plan is work out?
4. Whether complete closure for 8D analysis is document for future references? share with other members in the organization, so that learning are effectively utilize.
5. Whether tangible & intangible benefits are calculate? & included in the overall report?
And finally, you’ve got then the release and the signature of the author of the report and the final date of the closure. And once all 8D steps done, then the 8D analysis can be closed.
