Introduction
A wise man said that, “Your actions
decide your future, Isn’t it? ….. Yes, correct.
In industry we initiate the actions for improving our
process, therefore the conclusion based on fact and data is good for any
improvement. Now the question is that, why we need an improvement?
The automotive industry is dedicated for continual improvement. There is a law of nature, no one is identically same in the world, e.g. The Natural things such as Plants, Human beings, Animals, behavior etc. Or things that made by men such as shape of statue, diameter of rod, chemical & mechanical properties of materials etc. This change in similarity is due to the variation present in the manufacturing process, system, service and in real life. To eliminate /minimized the variation we need improvement in the process. By reduction in variation we will reduce the defect and improve the quality of product as well as save the cost. For the same we are committed for improvement by use of statistical methods.
So the application of statistical methods is to analyze the variation of process output and take appropriate actions to improve the process capability, quality of product and customer satisfaction.
The basic statistical methods include the statistical process control and process capability analysis. SPC is the core element of Production Part Approval Process (PPAP).
Why SPC?
Quality and SPC
From the beginning of time the concept of quality is with us. The quality of product is described by the terms strength, beauty or finish. For the mass production of product the dimension (size and shape) of product over time become a major quality issue. Therefore the quality obtains by inspecting the parts and passing those that met the specification. For the reason that process is monitored through sampling with the help of Statistical Process control (SPC) methods, by analyzing the results of samples actions taken on process before producing the defective parts from process.
Improve process–>better quality–>Reduce wastes–>Reduced costs
What is Statistical Process Control (SPC)
The concept of SPC methods were initially developed by Dr. Walter Shewhart of Bell Laboratories in the 1920’s, and were expanded upon by Dr. W. Edwards Deming, who introduce SPC to Japanese industry after the WWII. After early successful adoption by Japanese firms, Statistical Process Control has now been incorporated by organizations around the world as a primary tool to improve product quality by reducing process variation. Statistical process control is a collection of tools that when used together can result in process stability and variance reduction.
Understand the basics before going details for SPC;
- Decide actions: collecting, analyze & interpreting the data is not end of SP{C process. You have to take actions on basis of the study and increase the better understanding of process.
- Measurement System Analysis: Data collection by measurement system is the basis of SPC study, therefore measurement system is at acceptable condition before process data are collected for SPC study. To learn more about Measurement System Analysis (MSA).
- SPC can be applied to all area: At any area where the data is being measure and collected is applicable for the SPC analysis.
- Statistical Process control (SPC) is done on base of data being measure, the data is generally the parts (output of the process), so we are try to controlling our output by improving the process.
- If we learn details here still need some changes as per the actual practical applications with process control situations.
To learn about the SPC implementation cycle.
If you can’t measure it you can’t manage it.
Data
The data is the basics of SPC. In statistical techniques there is the analysis of samples and the data is collected by measurement of sample quantity. All processes are generating the data and this data is categorized as ‘Variable data’ and Attribute Data’.
1.Variable data: Also called as continuous data. Variable data is obtain by measurement using the measuring instrument.
Example: Diameter of rod, Width of block, Temperature, weight etc.
2. Attribute data: Also called as discrete data. This type of data is categorized with level or it is countable data.
Example: Count of students at each division, good – bad, Ok – Not ok etc.
Process control through SPC:
These two approaches are self-explanatory that we need. The Statistical Process Control (SPC) is for the prevention approach it means to avoid waste from the process.


Concept of Process Variation
As we discuss earlier, two objects/parts is not similar in nature, dimensions etc. The difference between them is due to the variation present in the process. To understand the process, to improve the process we need to identify the variation present in the process for that reason we need the SPC methods.
The process variations consist of two types:
1. Common cause variation
Any production process, regardless of how well designed or maintain it is, still there is a certain amount of inherent / natural / random variation will always exists. This variation is due to the many small, common unavoidable causes. Therefore the variation is called common cause variation. Common cause process is predictable and stable output. This type of variation can be minimizing by process experts and the management.
Example: Small variation in raw material quality, process parameter, environmental conditions, operator presence, small measurements and inspection errors etc.
2. Special cause variation
The systematic variation can occasionally, unexpectedly present in the output of the process and this type of variation due to the cause which is in different pattern than natural cause is called the special cause or assignable cause variation. Common cause process is unpredictable and not stable. This type of variation can be eliminated by shop floor experts.
Examples:
- Large variations in quality of raw materials
- Differences between batches of materials
- Unstable settings, Large differences between tools used
- Operator skill & training
- Large fluctuations in process parameter values from time-to-time
- Time related factors like tool wear, depletion of chemicals in a batch, operator attention etc.
- Large measuring errors due to use of inaccurate, imprecise instruments and gauges.
- Large fluctuations in environmental conditions (temperature, humidity, dust etc.)
Process Stability
What is stability?
The process is free from special cause and contain only common cause is a stable process. The stable process having a consistent pattern, process is repeatable and the quality of future product is predictable.
What is stability? —-> It is consistency
Why stability? —-> It is predictable. (Predictability)
How to assess the stability? —-> Using statistical principles

The statistical methods have the tools to verify the stability of the process. We are collecting the measurement data and verify the process using the statistical tools as listed below;
- Line / Run chart
- Histogram
- Control Charts
- Box plot
Measure data—>Record the data—>Represent in chart—>Analyze the data—>Take action

Process Capability
In the process capability we will verify that
- How good is the process
- Is the process capable of meeting the specification
- How to analyze the process
No two things will be alike due to presence of variation and it is the greatest enemy of any process as we discussed before. More than two third of our productivity time is waste to deal with variation. Therefore the variation in any process exhibits the process performance or process capability. Lesser the variation better is the capability.
Lets take example;
We are inspecting the diameter of hole which is being generated by punching operation, now to check the capability of the punching process you check the sample parts with diameter of hole each day and consistent for week. For this step each day is the subgroup for you. We observed that the variation observed in a day is small but the variation observed in the week is too large as compare to day. Therefore we take the term subgroup for calculating the process capability.


Standard Deviation (σ) = It is the variation in the process. Lesser the variation more the process is capable

Don’t be confuse about the term Cp-Cpk & Pp-Ppk. To learn more about the Difference between Process Capability(Cp) & Process Performance (Pp).
Process Capability Vs Tolerance
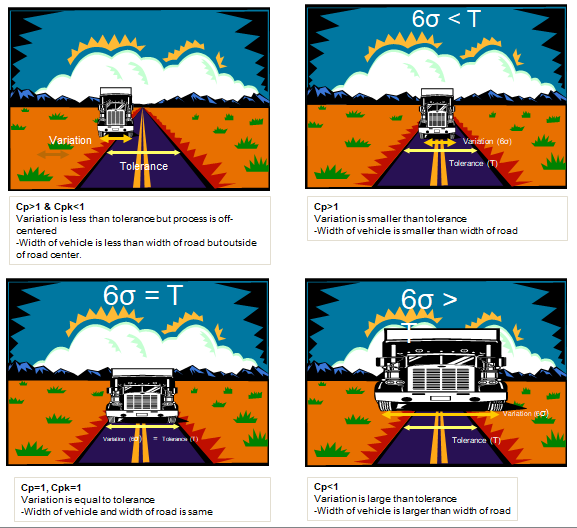


Steps for doing Process capability study
- Verify the process is stable (By using Control Charts)
- Determine if the data distribution is normal (Histogram)
- Calculate Process Capability (Cp & Cpk)
- Make recommendation for process improvement
Calculate the Process capability
There are two indices for calculating the process capability,
- The Cp is represent the spread of the distribution,

- The Cpk indices represent the center tendency of the process, It shows the process is capable as well as meet the specification as per requirement.

Summary of Statistical Process Control (SPC)
1.Take the parameter for the SPC. The parameter should be SC, CC, or customer specific requirement and take such parameter for the control in process.
2. Measurement System Analysis: MSA should be done before conducting the MSA because the variation in measurement system contributes the failure of the results from SPC.
3. Measure the sample data for measurement (Lot wise, subgroup wise) so that we can compare it to the population & consider for the SPC study.
4. Analyze the data using the statistical tools, so that we verify that the process is stable or not. If process is stable then go for next.
5. Calculate the process capability indices (Cp, Cpk) or Process Performance indices (Pp, Ppk) to analyze the process spread and location.
6. On the base of result make improvement in the process and monitored for the future to avoid the defective parts production.