ISO 9001:2015 is the international standards developed for manufacturing industry. We can say it is a certain criteria that every organization should follow to maintain their importance in market as a standard company.
After achieving this certification your company will be the one who focus on product quality and quality management system (QMS) to enhanced customer satisfaction.
In this guide we will se what ISO 9001:2015 is and how to implement it align with all steps to get the ISO certification.
Lets get started.
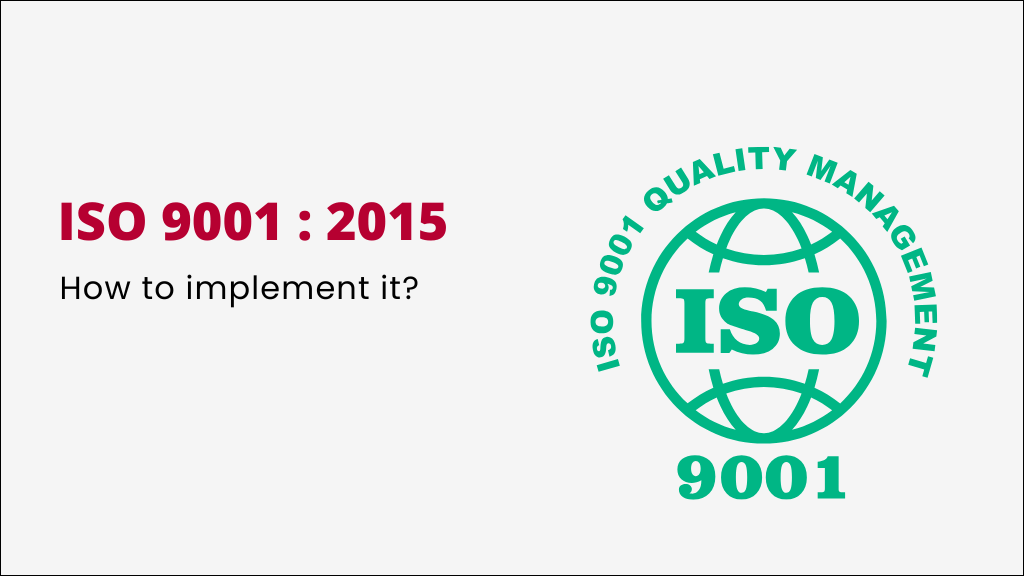
What is ISO 9001:2015?
Firstly the meaning of ISO is International Organization for Standardization.
Now this International organization has created a 9000 series of standards, and ISO 9001 is one of them. You can have look on below chart of all series of standards for your understanding.
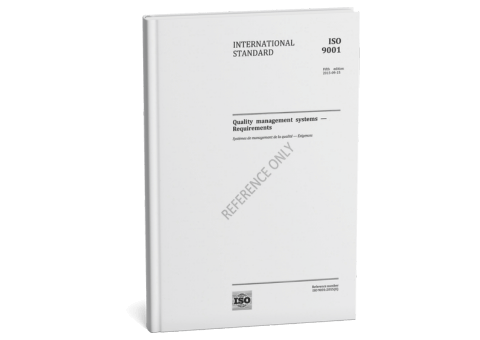
Here ISO 9001 is a set of standard rules or framework developed for any company who wants to improve their quality processes and meet customer as well as regulatory requirements. To achieve better quality and customer satisfaction your company should follow and implement this standard.
Now ISO 9001:2015 is the updated version of this standard which released in year of 2015.
You can also have a look on previous versions.
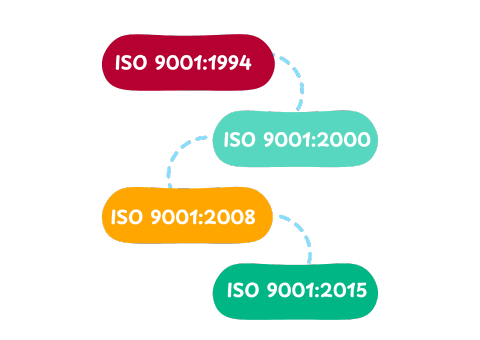
ISO 9001:2015 update is mainly focused on customer satisfaction, risk based thinking, leadership involvement, process based approaches, and continual improvement in your company.
ISO 9001 is not the case that solve every problem of your company but it provides certain guidelines to improve your product and processes.
Why ISO 9001:2015 matters for Manufacturing companies?
A manufacturing company will be successful when they produced a high-quality parts, which meets customer requirements. This leads to have a good customer satisfaction and then the company have a good reputation in market.
This all happens when company follows industry-specific standards, managing supplier relationships along with improving their processes to have low wastes.
ISO 9001:2015 is very important to achieve all above criteria, therefore it matters most to manufacturing companies.
You can have a look on reasons below to clarify you that why ISO standards matters.
Improved Product Quality: This standard helps companies to ensure products consistently meet customer specified requirements.
Increase Process Efficiency: ISO 9001 is the standard for quality management system. Therefore, it helps companies to focuses on process base approach and which ultimately help to reduced defects, delays and rework in your production processes.
Customer Satisfaction: When you follow ISO standard it will help you to achieved customer requirement. And as a result, your customer will satisfied by meeting customer needs and expectations.
Risk Management: ISO suggest implementing risk analysis tools such as FMEA to identify potential issues during development. This helps to address and take action on those issues before they occur in future.
Global Recognition: ISO standard common for all global companies. Therefore, your certification has global credibility, and you can enter into international business and able to provide parts to many international companies and OEMs.
Core Principles of ISO 9001:2015
ISO 9001:2015 standard is built on seven core principles below:
1. Customer Focus: Understand your customer requirements, focus to meet those requirement/specification and try to exceed their expectations.
2. Leadership: We all know the strong leadership guide your company well and get success. Create a quality culture and it is drive by company leadership by providing clear guidelines and directions.
3. People Engagement: Leadership gives you the direction and guideline but without people involvement and engagement it won’t possible to achieve the success. Therefore, everyone should involve and put their efforts to achieve organization goal.
4. Process Approach: Every activity is a process, therefore managing those activities as processes leads to better efficiency and effectiveness.
5. Improvement: Management and all employees should be committed for continual improvement into QMS.
6. Evidence-Based Decision Making: Collect and analyze data then take action which is Data driven decision making.
7. Relationship Management: Build strong relationships with all stakeholders for example customer, suppliers and business partners.
In addition, ISO recommend to use the PDCA (Plan-Do-Check-Act) methodology in your quality management system processes to enhance the QMS.
“Markets change, tastes change, so the companies and individuals who choose to compete in those markets must change” ——– An Wang
ISO 9001:2015 Structure and Key Clauses
ISO 9001:2015 contains a High-Level Structure with 10 clauses. Clauses 1 to 3 are general information, where Clauses 4 to 10 are auditable and contain the key requirements for certification.
Non-auditable clauses
1st Clause: Scope
2nd Clause: Normative References
3rd Clause: Terms and Definitions
Auditable clauses
Clause 4: Context of the Organization
This clause says that organization should understand internal and external issues. Those issues can affect your company goals and QMS. If you identify those issues earlier then it helps to achieve desire results of QMS.
Clause 5: Leadership
In this clause, it requires top management to focus on providing a guideline and create a quality culture in company. It involves the leadership and commitment for customer focus, company objectives, quality policy and business goals.
Clause 6: Planning
Planning clause includes a risk-based thinking approach in QMS to identify and prevent issues. Considering actions to address issues, objective planning and change planning.
Clause 7: Support
Once you have done planning then to execute you need support in the form of resources. Therefore, it involves resources, infrastructure, peoples, and effective communication.
Clause 8: Operation
This is the largest section of Quality Management System. Which focus on control of product, process and service. It considers the factors includes requirements, planning, development, supplier product and processes, production, delivery and service.
Clause 9: Performance Evaluation
Here you need to monitor, measure, and evaluate QMS performance by analyzing data, performing audits and management reviews.
Clause 10: Improvement
Improvement is the key principle of ISO 9011:2015 QMS. It focuses on continual improvement, finding nonconformities and opportunities to improve.
Steps to Implement ISO 9001:2015 in a Manufacturing Company
Implementing ISO 9001:2015 quality management system need leadership or management commitment and support. But this only support will not helps until entire the involvement of employees and QMS coordinators.
Using following step-by-step approach you can implement the ISO standard among organization.
1. Gap Analysis
1st step is to understand your current processes. Then compare those processes with ISO 9001 standard requirements. This will help to identify the gaps of what you are doing and what standard ask to do.
2. Leadership Commitment
As we said before the top management and leadership support is must for implementation of this system. They should be fully involved in QMS activities.
3. Training and Awareness
Training is important factor for successful implementation of Iso standard. This involves the training of internal quality auditors. Provide awareness training of ISO 9001:2015 to employees so that they can understand all standard requirement and involved in implementation activity.
The training helps to create the internal auditors in your organization who further take care of all processes by conducting internal audits.
4. Developing Documentation
Developing documents means to create the required QMS documents and formats as per standard guidelines.
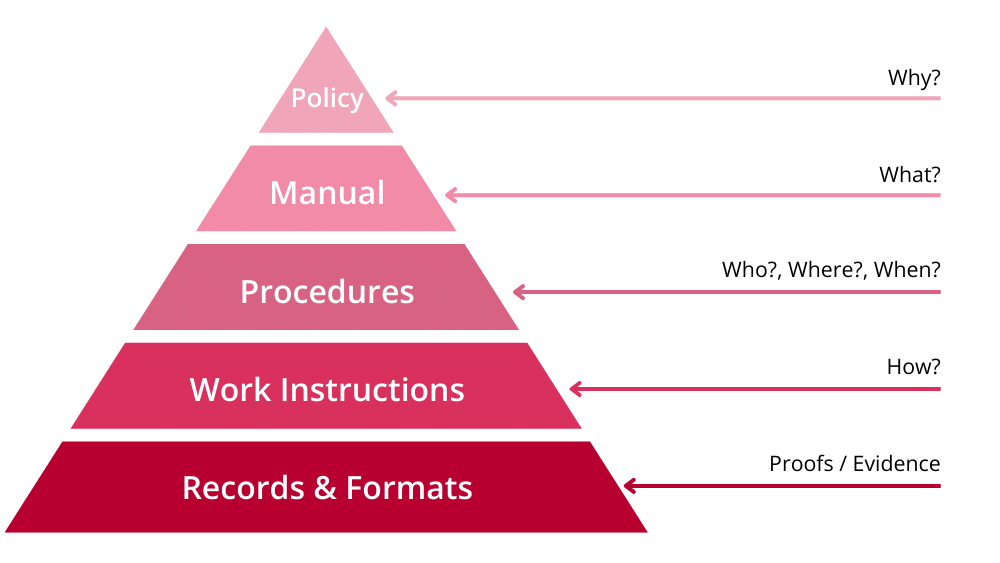
Every organization should have a common documents structure as per ISO 9001:2015 standard. Which includes objectives, Quality Policy, Quality Manual, Procedures, work instructions and records.
5. Risk-Based Thinking
This is the key approach of ISO standard, therefore while implementing ISO every organization should focus on identifying potential risks in their processes and implement a preventive measure to reduce the risk.
6. Process Control
Process approach tells us to standardize and monitor or processes. This helps to find out the trend and area for continual improvement. This leads to have better process, better product and improves customer satisfaction.
7. Internal Audits
Regular audits as per plan helps internal processes to be compliant and effective. It helps to identify issues and support improvement activity in organization.
8. Management Review
Once all activities done, a management review should conduct to review all things related to QMS. Here management will have a look on all points related to documentation and process results considering audit results and effectiveness.
Management also checks that the ISO 9001:2015 QMS remains implemented or not and are this align with our organizational goal or not.
9. Prepare for Certification Audit
Once one cycle completes with all above points, then your organization should eligible or capable for certification audit. This certification audit done by external certification agencies, who do the certification audit and based on passing criteria they will provide you the ISO 9001:2015 certification.
For that you need to approach to one of the certification body and plan for audit.
Certification Process
Once you decide to become a ISO 9001 certified manufacturing company, you need to face the audit from an external accredited certification body.
The audit done on both documentation part as we as on-site shop floor verification.
Stage 1: Documentation Audit
The auditor will review and verify all your documents and records to check that is it align with ISO 9001 standard or not.
Stage 2: On-site Audit
On-site verification involves audit of your operations on production line. The auditor will check your production processes following all procedures and standards what mentioned in ISO requirements.
If auditor find any problems then they will simply give you the non-conformity (NC). You must close the NC’s by providing action plan. Then the certification body will decide that you have pass or failed in audit.
If the audit is successful, then the certification body will issue a ISO 9001:2015 certification. This certification will be valid for 3 years. In between yearly a surveillance audits conducted to check that are you continually following the standard or not.
Benefits of ISO 9001:2015 Certification for Manufacturing Companies
Once you got certification you will have now lot of benefits as a manufacturing company.
Competitive Advantage: Almost all international and OEM’s works with all ISO 9001 certified companies only. Therefore, they prefer to work with you if you are a ISO 9001 certified company.
Operational Consistency: Best and standard processes leads to have a smooth operation in your company.
Regulatory Compliance: Helps to reduces the risk of legal issues as you have take care proactively.
Increased Employee Engagement
Good Financial Performance
Common Challenges and Solutions in Achieving ISO 9001:2015 Certification
You think it is simple process but not, many companies facing lot of challenges. These three are most of them.
Lack of Commitment from Leadership: Leadership will not involve in many processes such as defining objective and creating guidelines for company.
Insufficient Resources or Training: Lack of resources and training will leads to no or partial involvement of team to implementation. Results in failing to adapt this quality management system.
Resistance to Change: The implementation of ISO 9001 is one of the big changes in your organization. Many peoples are not wanting to adopt this change due to adding additional system and processes. But this is a good change and helps to improve your organizational performance and efficiency.
Conclusion
ISO 9001:2015 certification is one of the strategy of any manufacturing company to implement a Quality Management System. It helps to improve product, process quality along with adapting a continual improvement culture. This ultimately improves existing customer satisfaction. Also helps to get new customers as you are now a ISO 9001 certified company.

I am a full time Engineer and Quality Professional with over 11+ years of experience in the automotive industry. My professional journey has started from a small enterprise quality inspector to a advanced quality expert. I am creating a good-quality content for engineers. Help them to grow in their career.Learn more here.