In today’s competitive manufacturing business, leadership plays important role in to have success of an organization. Leaders are not just responsible to manage teams but also create a culture of continuous improvement, good work environment, and high quality standards.
Dr. W. Edwards Deming provide a best framework for leadership in manufacturing sector. He is known for one of the Quality Guru. His 14 points of management helps industry leaders to make efficient, effective and quality-driven organization.
In this article, you will have an idea of the importance of leadership in manufacturing domain, including a detailed view of Deming’s 14 Points, and how these principles can help organizations to improve their processes, enhance quality, and lead with purpose.

The Role of Leadership in Manufacturing
Leadership in manufacturing it’s not just about giving instructions and expect results they should focus on principles. It’s about more focus on creating a culture of collaboration, continuous improvement, and accountability.
Good leadership has a power to coordinate entire organization with common goals. Those goals such as improving product quality, reducing waste, and increasing customer satisfaction.
A leader’s role in manufacturing involves:
- Set a vision: Create clear, realistic goals that match the organization’s overall direction.
- Promote a quality-focused culture: Build a mindset of quality in every process.
- Build trust: Encourage open communication and teamwork.
- Enable continuous improvement: Support learning and development to stay ahead.
- Support change: Help teams adjust to new technologies, processes, and standards.
Deming’s Influence on Leadership
Dr. W. Edwards Deming was a leader in promoting quality improvement in manufacturing.
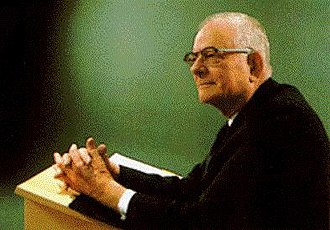
He focus on long-term success. And its not about problem solving. Its about building a company which has a good leadership and culture that focus on preventing the problems before they happen.
His 14 Points of Management guide all leaders to create this kind of culture and to manage quality and productivity with involvement of employees and satisfaction.
Deming’s 14 Points of Management
1. Create constancy of purpose for improving products and services
Our organization leadership should be focus on improving quality, reducing costs, and to meet customer needs.
In manufacturing, this means not just focusing on the next quarter’s profits but should have a long term focus.
Application: A leader should set clear goals for continuous improvement, invest in innovation, research and development to meet changing customer demands and technological advancements.
2. Adopt the new philosophy
Every organization should shift their focus towards quality culture.
Leadership should understand that old way of working and doing things may not be effective in this competitive and fast changing world.
Application: In the manufacturing domain, leaders must implement lean manufacturing, digital transformation, and data-driven decision-making. Resistance to change can lead to outdated from the market condition.
3. Cease dependence on inspection to achieve quality
Old way of quality control method is depends on inspections. Deming suggested that this is not effective method to ensure quality because it can only find out the errors after they occur.
Application: Organization should focus on robust process design that prevent defects from happening at first place. This involve better training, using statistical process control methods, and ensuring quality at every stage of production.
4. End the practice of awarding business on price alone
Deming says that supplier selection based on only lower cost is a short term approach. Instead, organization should focus on long term relationship which ensures the supplier will deliver consistent quality and service of their products.
Application: Leaders in manufacturing should threat suppliers as partners and stakeholder. They should work closely with supplier to improve the product quality and continuous improvement. This helps to build supplier capability to deliver good quality product consistently.
5. Improve constantly and forever the system of production and service
Continuous improvement (Kaizen) is a key topic of Deming’s philosophy. Leaders should keep eye on improvements in all areas, such as production, services, and overall management.
Application: By implementing a Kaizen culture, manufacturing leaders motivate their teams to find out the ways to improve processes, reduce waste, and increase efficiency. This can be possible by conducting regular reviews, employee suggestions, and upgrading to new technologies.
6. Institute training on the job
Every organization need a well trained people to achieve highest quality products. Therefore Demings believed that organization should invest in peoples to train them a good skills and knowledge.
Application: In manufacturing, leaders should ensure that employees get proper on-the-job training, specifically the areas such as new machinery, software, or quality control methods. Cross-training employees to handle multiple roles can also improve flexibility in work and reduce downtime.
7. Institute leadership
Managers are already act as supervisors but more than that they should act as coach. Their role is to guide and support their teams to do better job.
Application: In manufacturing, leaders not just giving orders but working with teams to solve problems, improve processes, and ensure safety and quality. Leaders should be approachable, listen team’s concerns, and help them to find a solutions.
8. Drive out fear
Fear in workplace creates poor communication, lack of creativity, and lower morale. Employees should feel safe to present their ideas, problems, and offer suggestions without fear of punishment.
Application: Manufacturing leaders should create a culture where employees feel valued and heard. They should open for communication and listening feedback. This helped positive work environment and culture among the team.
9. Break down barriers between staff areas
Don’t focus on work to be done by a single department or work in silos. Which is not good and inefficient. Every organization should work on cross-functional team approach.
Application: Leaders in manufacturing should work as cross-functional teams and collaboration between many departments for example engineering, production, quality control, and logistics. By working together, they can solve problems faster.
10. Eliminate slogans, exhortations, and targets for the workforce
Deming believed that slogans and targets creates frustration and don’t focusses on root cause of any problem. Therefore organization should focus on creating and improving system rather than slogans and targets.
Application: In manufacturing, organization just creating slogans of “zero defects and zero customer complaint”, rather than trying to built systems and solve problems to create good quality product.
11. Eliminate numerical quotas and management by objectives
Performance evaluation should not be only depends on meeting numbers and targets. This creates wrong behaviors and leads people priority to quantity over quality.
Application: Leaders should focus on quality, collaboration, and improvement rather than meeting targets and numbers. This might be the new ways to measure success, example as customer satisfaction, defect rates, or time saved in production.
12. Remove barriers that rob people pride in their work
Employees should be proud of their work contributions and achievements. When some barriers like poor processes or impossible targets leads to employees frustrated and feel unmotivated.
Application: In manufacturing, leaders can remove these barriers. Provide adequate training, setting realistic targets and expectations.
13. Encourage education and self-improvement for everyone
Leaders should provide the opportunity of learning and personal development for everyone. This helps team growing personally and professionally.
Application: In manufacturing, leaders should provide educational opportunity, such as certifications, workshops, or training on new technologies. This investment in people leads to a more knowledgeable and competent workforce for the organization.
14. Take action to accomplish the transformation
Finally, Deming’s last point guide us for a commitment to change. Leaders should lead by example.
“Manage the top line: your strategy, your people, and your products, and the bottom line will follow.” —– by Steve jobs
Key Takeaways for Manufacturing Leaders from Demings 14 points
- Prioritize Quality: The success of any manufacturing organization will be depend on their ability to deliver consistent quality products. Leaders must take quality as a top priority, not just in words but in actions, investments, and everyday work and processes.
- Foster a Culture of Continuous Improvement: The manufacturing industry is evolves and constantly changing therefore leaders should adapt the mindset of continuous improvement. This involves being open to new ideas, adopt new technologies, and continuously find out the ways to improve processes.
- Empower Employees: Leadership should understand their team and improve their performance by providing necessary trainings, solve their problems, have a good collaboration. This helps to improve organization progress.
- Build Long-Term Relationships with Suppliers: Supplier provided part quality directly impacts your product quality. Leaders should develop long-term relationships with trusted suppliers so that they can provide consistently good , and high-quality materials.
- Lead by Example: Leadership is about setting the role model for the organization. Using these principles leaders are the one who lead with integrity, manufacturing leaders can create an environment where quality, efficiency, and employee satisfaction go hand in hand.

I am a full time Engineer and Quality Professional with over 11+ years of experience in the automotive industry. My professional journey has started from a small enterprise quality inspector to a advanced quality expert. I am creating a good-quality content for engineers. Help them to grow in their career.Learn more here.